Semiconductor device manufacturing method and substrate treating apparatus
A technology of substrate processing device and manufacturing method, which is applied in the direction of semiconductor/solid-state device manufacturing, electrical components, circuits, etc., and can solve the problem of polluting the surface of the wafer
- Summary
- Abstract
- Description
- Claims
- Application Information
AI Technical Summary
Problems solved by technology
Method used
Image
Examples
Embodiment 1
[0176] Next, as a first example, in order to prove SiH 4 The temperature dependence and pressure dependence of the surface oxygen density (concentration) during purification will be described by experiments.
[0177] An example of a semiconductor device requiring a low oxygen density interface is an electrode portion drawn from a source and a drain of a DRAM (Dynamic Random Access Memory). This interface characteristic is called contact resistance, and the smaller the amount of natural oxide film in this part, the lower the contact resistance and improve the electrical characteristics.
[0178] As the evaluation test of this example, aiming at electrical characteristics, D-polySi film (phosphorus-doped polysilicon film) and D-polySi film (phosphorus-doped polysilicon film) were measured by SIMS (Secondary Ionization Mass Spectrometer) interface properties between them.
[0179] In addition, as the evaluation device, the device of the above-mentioned embodiment, that is, a fi...
Embodiment 2
[0204] Next, as a second example, in order to prove SiH 4 The temperature dependence of the purified contact resistance for experiments is described.
[0205] In the second embodiment, based on the SIMS evaluation results of the first embodiment, the interface contact resistance evaluation is carried out using actual equipment.
[0206] Due to the SIMS results according to the first example, SiH at low temperature and high vacuum 4 Purification is effective, so the evaluation was carried out by using TMP with the pressure fixed at 10 Pa, and at two temperatures, 330°C and 430°C, which are lower than the film formation temperature (530°C).
[0207] Figure 4 Indicates the interfacial contact resistance for SiH 4 Dependence of purification temperature.
[0208] The horizontal axis represents SiH 4 Purification temperature (°C), vertical axis represents interface contact resistance (Ω / piece).
[0209] As mentioned above, changing the SiH 4 The purification temperature was ...
Embodiment 3
[0213] Next, as a third example, in order to prove SiH 4 Purified interfacial oxygen density vs. wafer entering furnace to entering SiH 4 The time dependence of the completion of the purification step is illustrated by the experiments performed.
[0214] Figure 5 Indicates the interface oxygen density vs. from the end of the wafer into the furnace to SiH 4 Dependence of time for completion of the purification step (SIMS results).
[0215] The horizontal axis represents the time from the end of the wafer into the furnace to the SiH 4 The time for the completion of the purification step (minutes), the vertical axis represents the interface oxygen density (atoms / cm 2 ).
[0216] Such as Figure 5 As shown, will be from furnace to SiH 4 The time to complete the purification step was changed to 50 minutes and 15 minutes for evaluation.
[0217] according to Figure 5 It can be seen that from the furnace to the SiH 4 When the time to complete the purge step is short, the ...
PUM
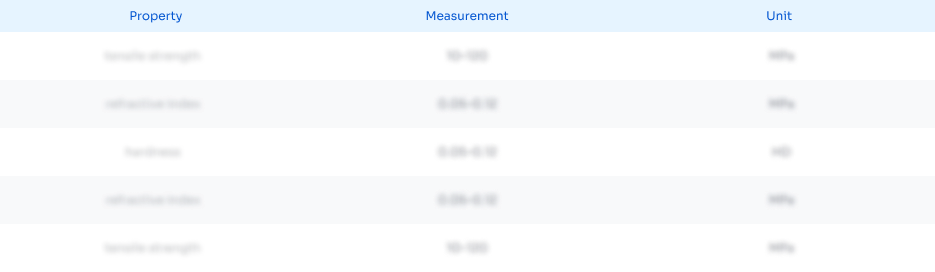
Abstract
Description
Claims
Application Information

- R&D Engineer
- R&D Manager
- IP Professional
- Industry Leading Data Capabilities
- Powerful AI technology
- Patent DNA Extraction
Browse by: Latest US Patents, China's latest patents, Technical Efficacy Thesaurus, Application Domain, Technology Topic, Popular Technical Reports.
© 2024 PatSnap. All rights reserved.Legal|Privacy policy|Modern Slavery Act Transparency Statement|Sitemap|About US| Contact US: help@patsnap.com