Finishing monoblock for a billet lamination plant for producing high-quality wire rods
A technology for laminating equipment and production lines, which can be used in driving devices for metal rolling mills, metal processing equipment, manufacturing tools, etc., and can solve problems such as large output loss
- Summary
- Abstract
- Description
- Claims
- Application Information
AI Technical Summary
Problems solved by technology
Method used
Image
Examples
Embodiment Construction
[0042] Referring to Figures 4 to 9 and 19, 20, the finishing unit for the blank lamination plant comprises at least a first module M1 and a second module M2', M2".
[0043] Modules M1, M2', M2" comprise a plurality of lamination hoods G1, G2, G3, Gn adapted to form a sequential arrangement of a lamination line for laminating incoming blanks in the direction indicated by arrow F in order to manufacture Sectional wire or generally laminated products.
[0044] These modules comprise two parallel mechanical transmissions, a first transmission 22 and a second transmission 22', which in turn are connected and actuated by at least one control reducer 23 arranged downstream of the second module M2', M2". The control reducer 23 is connected to the running drive motor 25 arranged in series with the whole unit through a gear 24.
[0045] The mechanical transmission 22, 22' is equipped with pairs of bevel gears 26 and gears 27, which transmit rotation in series to the respective housings...
PUM
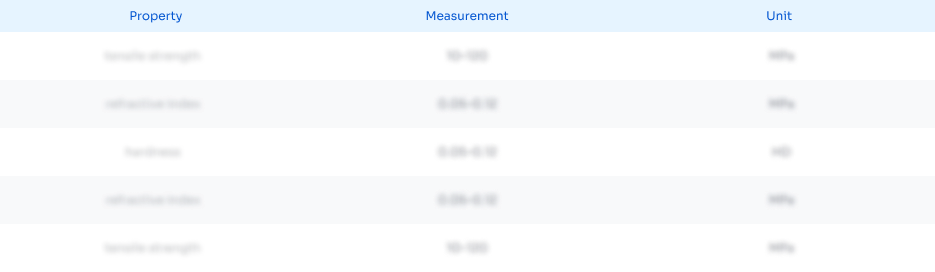
Abstract
Description
Claims
Application Information

- R&D Engineer
- R&D Manager
- IP Professional
- Industry Leading Data Capabilities
- Powerful AI technology
- Patent DNA Extraction
Browse by: Latest US Patents, China's latest patents, Technical Efficacy Thesaurus, Application Domain, Technology Topic, Popular Technical Reports.
© 2024 PatSnap. All rights reserved.Legal|Privacy policy|Modern Slavery Act Transparency Statement|Sitemap|About US| Contact US: help@patsnap.com