Process of producing Zn-Cu-Ni alloy strip
A production method, zinc-nickel-nickel copper technology, applied in the production field of C7701 strips, can solve the problems of easy discoloration of the product and affect the quality of the finished product, achieve the effect of unchanged color, solve the problem of discoloration, and improve high temperature resistance
- Summary
- Abstract
- Description
- Claims
- Application Information
AI Technical Summary
Problems solved by technology
Method used
Examples
Embodiment 1
[0016] Embodiment 1: Casting, face milling, rough rolling, intermediate annealing, cleaning, intermediate rolling, edge trimming, intermediate annealing, finishing rolling, degreasing cleaning, annealing, tension bending straightening, surface treatment, strip warehousing of raw materials, the The above annealing process is to keep the temperature at 350° C. for 6 hours under a hydrogen protective atmosphere with a volume concentration of 30%.
Embodiment 2
[0017] Embodiment 2: Except that the annealing process is under a hydrogen protective atmosphere with a volume concentration of 50%, at 370° C. for 7 hours, the rest is the same as in Embodiment 1.
Embodiment 3
[0018] Embodiment 3: except that the annealing process is under a hydrogen protective atmosphere with a volume concentration of 70%, at 390° C. for 8 hours, the rest is the same as in Embodiment 1.
PUM
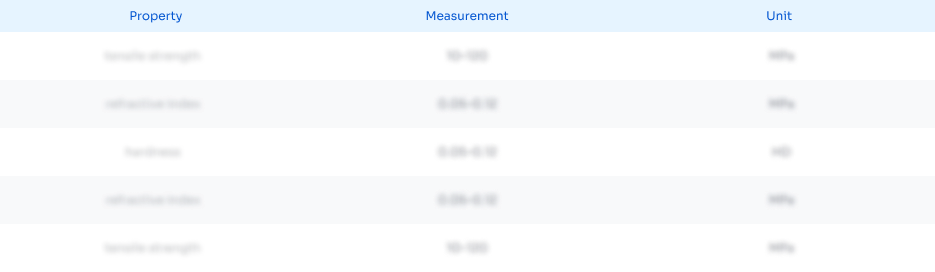
Abstract
Description
Claims
Application Information

- R&D
- Intellectual Property
- Life Sciences
- Materials
- Tech Scout
- Unparalleled Data Quality
- Higher Quality Content
- 60% Fewer Hallucinations
Browse by: Latest US Patents, China's latest patents, Technical Efficacy Thesaurus, Application Domain, Technology Topic, Popular Technical Reports.
© 2025 PatSnap. All rights reserved.Legal|Privacy policy|Modern Slavery Act Transparency Statement|Sitemap|About US| Contact US: help@patsnap.com