Miniature car front frame skeleton structure
A skeleton structure and front frame technology, applied in load-bearing body structures, superstructures, substructures, etc., can solve the problems of increasing the weight of the body assembly and material costs, unfavorable use of mini cars, and large cross-sectional dimensions, etc., to save materials and space, good rigidity and strength, and small cross-sectional size
- Summary
- Abstract
- Description
- Claims
- Application Information
AI Technical Summary
Problems solved by technology
Method used
Image
Examples
Embodiment Construction
[0013] see figure 1 , the front frame skeleton structure is composed of the left and right longitudinal beam welding assemblies 3 and 4, the front collision beam welding assembly 1, the front beam welding assembly 2 and the front wall support beam welding assembly 5 to form a complete receiving force frame. see Figure 4 It can be seen that the left and right longitudinal beam welding assemblies 3 and 4 are "Z"-shaped structures made of high-strength steel plates. Depend on figure 2 and image 3 It can be seen that the front collision beam welding assembly 1 and the front cross beam welding assembly 2 adopt a closed section, and the front cross beam welding assembly 2 is composed of a front cross beam 31 and a front cross beam left connector 32 and a front cross beam right connector 33 welded at both ends. . For the structure of the welding assembly 5 of the front wall support beam, see Figure 5 , the front panel support beam 51 and the front panel front panel strength...
PUM
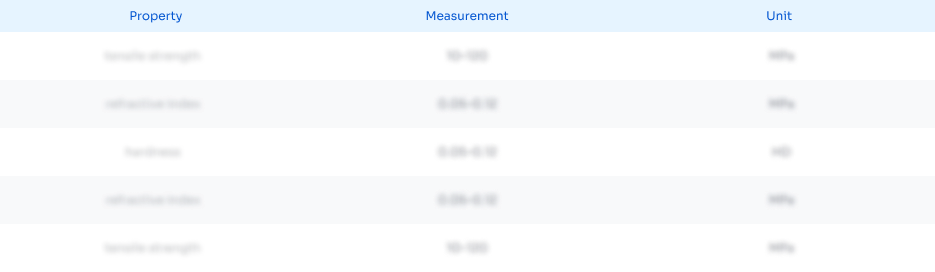
Abstract
Description
Claims
Application Information

- R&D
- Intellectual Property
- Life Sciences
- Materials
- Tech Scout
- Unparalleled Data Quality
- Higher Quality Content
- 60% Fewer Hallucinations
Browse by: Latest US Patents, China's latest patents, Technical Efficacy Thesaurus, Application Domain, Technology Topic, Popular Technical Reports.
© 2025 PatSnap. All rights reserved.Legal|Privacy policy|Modern Slavery Act Transparency Statement|Sitemap|About US| Contact US: help@patsnap.com