Three section type catalystic conversion method of petroleum hydrocarbon raw material and its device
A petroleum hydrocarbon, three-stage technology, applied in catalytic cracking, petroleum industry, cracking, etc., can solve the problems of high energy consumption of catalyst transportation, unfavorable regeneration, etc., and achieve the effect of improving product quality, improving quality, and improving upgrading effect
Inactive Publication Date: 2008-06-11
洛阳石化设备研究所
View PDF9 Cites 0 Cited by
- Summary
- Abstract
- Description
- Claims
- Application Information
AI Technical Summary
Problems solved by technology
These low-carbon, low-temperature, high-activity catalysts in the prior art are not utilized, but directly enter the regenerator, which is not conducive to regeneration
In the existing technology of separate cracking of recycled oil and raw oil, since the height of the required riser reactor is only about half of the conventional one, it is necessary to build another catalyst container similar to a regenerator to transport the regenerant to a certain height in order to provide the reaction riser. Supply agent, catalyst transportation energy consumption is also high
Method used
the structure of the environmentally friendly knitted fabric provided by the present invention; figure 2 Flow chart of the yarn wrapping machine for environmentally friendly knitted fabrics and storage devices; image 3 Is the parameter map of the yarn covering machine
View moreImage
Smart Image Click on the blue labels to locate them in the text.
Smart ImageViewing Examples
Examples
Experimental program
Comparison scheme
Effect test
Embodiment 2
[0030] Embodiment 2. In this embodiment, in the catalytic cracking reaction section of the heavy oil reactor 100, the recycled oil riser 2 is arranged inside the raw oil riser 1, and both share a regeneration riser 72A and a regeneration slide valve 74A. 23 enters at the bottom. Others are the same as embodiment 1.
the structure of the environmentally friendly knitted fabric provided by the present invention; figure 2 Flow chart of the yarn wrapping machine for environmentally friendly knitted fabrics and storage devices; image 3 Is the parameter map of the yarn covering machine
Login to View More PUM
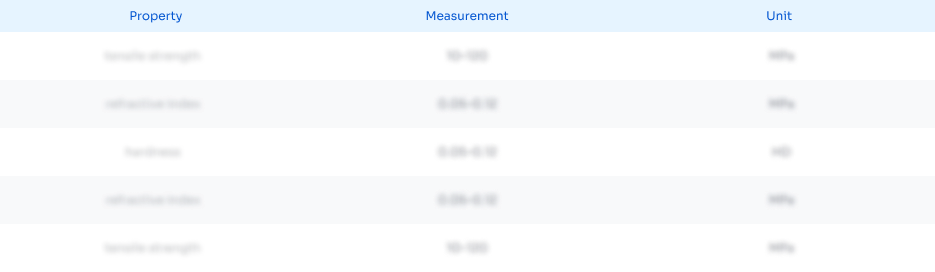
Abstract
The invention relates to a three-stage petroleum hydrocarbon raw material catalytic conversion method and the reactor thereof, belonging to petroleum hydrocarbon catalytic conversion process field. And the method makes raw oil, back-refined oil, and gasoline react separately and not interfere with one another; the catalytic cracking reacting region of a heavy oil reactor uses regenerated catalyst, and the modifying reacting region supplements low temperature catalyst after gasoline reaction, forming second reacting region; after the gasoline reaction ends, the extracted catalyst is fed into the second reaction region of heavy oil reaction and continues being used; the gasoline reaction and back-refined oil cracking reaction adopt regenerated catalyst temperature lowering solution, implementing high solvent-oil ratio working condition. And the reactor is a combined reactor composed of heavy oil reacting part and parallel and interconnected gasoline reacting parts. And it separately refines different materials and makes gasoline and heavy oil cooperate with each other and their advantages complementary; and raises reacting efficiency and improves product quality.
Description
technical field [0001] The invention belongs to the technical field of catalytic conversion process devices for petroleum hydrocarbons, in particular to a three-stage catalytic conversion method for petroleum hydrocarbon raw materials producing clean fuel oil from petroleum hydrocarbon raw materials with high conversion rate and producing gasoline with low olefin and low sulfur content and devices. Background technique [0002] The fluid catalytic cracking process has gone through 60 years of development and has made great achievements and technological progress. The development of society makes the requirements for this process continuously increase, especially in terms of environmental protection, which poses new challenges to the catalytic cracking process, that is, not only to achieve economic benefits but also to meet the requirements of environmental protection. Gasoline standards in developed countries require olefins to be below 18% (weight) and sulfur content to be...
Claims
the structure of the environmentally friendly knitted fabric provided by the present invention; figure 2 Flow chart of the yarn wrapping machine for environmentally friendly knitted fabrics and storage devices; image 3 Is the parameter map of the yarn covering machine
Login to View More Application Information
Patent Timeline

Patent Type & Authority Patents(China)
IPC IPC(8): C10G11/00
Inventor 石宝珍
Owner 洛阳石化设备研究所
Features
- R&D
- Intellectual Property
- Life Sciences
- Materials
- Tech Scout
Why Patsnap Eureka
- Unparalleled Data Quality
- Higher Quality Content
- 60% Fewer Hallucinations
Social media
Patsnap Eureka Blog
Learn More Browse by: Latest US Patents, China's latest patents, Technical Efficacy Thesaurus, Application Domain, Technology Topic, Popular Technical Reports.
© 2025 PatSnap. All rights reserved.Legal|Privacy policy|Modern Slavery Act Transparency Statement|Sitemap|About US| Contact US: help@patsnap.com