Rotating magnetic field type driver for active controlling torsional vibration of rotational axis system
A rotating magnetic field, active control technology, applied in the direction of suppressing motor vibration control, mechanical vibration control, non-electric variable control, etc., can solve the problems of complex structure and difficult implementation.
- Summary
- Abstract
- Description
- Claims
- Application Information
AI Technical Summary
Problems solved by technology
Method used
Image
Examples
Embodiment Construction
[0009] The structure of the present invention will be further described below through specific embodiments and in conjunction with FIG. 1 and FIG. 2 . Motor 1 adopts a three-phase squirrel-cage motor with extended shaft, bearing 2-1 and bearing 2-2 are ball bearings, two supports 3-1, 3-2, coupling 4, stator rotating rod 5, and connecting rod 6 For general machining parts. The linear vibrator 7, the power amplifier 8, and the frequency converter 10 are all general products. Computer 14 adopts industrial control computer, and computer interface board 9 internal circuit block diagrams are as shown in Figure 3, and the circuit chip that computer interface board 9 adopts is as follows: speed counter 19 selects Intel 8254 for use; Filter amplifier 16 selects op07 for use; Exciting signal D / A converter 17 and motor speed regulating D / A converter 20 use dac1210; speed A / D converter 18 and torsional vibration A / D converter 21 use ad574. The computer interface board 9 is installed in...
PUM
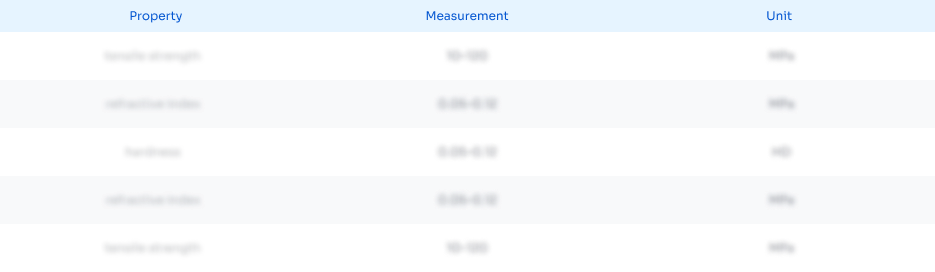
Abstract
Description
Claims
Application Information

- R&D
- Intellectual Property
- Life Sciences
- Materials
- Tech Scout
- Unparalleled Data Quality
- Higher Quality Content
- 60% Fewer Hallucinations
Browse by: Latest US Patents, China's latest patents, Technical Efficacy Thesaurus, Application Domain, Technology Topic, Popular Technical Reports.
© 2025 PatSnap. All rights reserved.Legal|Privacy policy|Modern Slavery Act Transparency Statement|Sitemap|About US| Contact US: help@patsnap.com