Cut-fracted oil oxidation desulfurizing method
A technology for oxidative desulfurization and distillate oil, which is applied in the direction of refining with oxygenated compounds, and can solve the problems of high cost, unsafe operation and environmental protection, and low mass transfer efficiency.
- Summary
- Abstract
- Description
- Claims
- Application Information
AI Technical Summary
Problems solved by technology
Method used
Image
Examples
Embodiment 1~3
[0035] This example proves that the use of reaction equipment with high mass transfer efficiency can significantly improve the desulfurization efficiency. Experimental process and experimental raw material are the same as comparative examples 1~3, just react and carry out in the impingement flow reactor identical with Fig. 2 structure, adopt two propellers, propeller rotating speed is 900 rev / mins, intermittent operation, reaction temperature drops to 70°C. The reaction raw material oils of Examples 1-3 correspond to Comparative Examples 1-3 respectively. The sulfur content analysis data of the reaction products are also listed in Table 1.
[0036] The test result of table 1 example 1~3 and comparative example 1~3
[0037] example
[0038] Apparently, under the same raw materials and other reaction conditions, using an impingement flow reactor with higher mass transfer efficiency can significantly increase the desulfurization rate of the oxidation reaction, and the...
Embodiment 4
[0040] Embodiment 4 is according to embodiment 1 process, and reaction temperature is 75 ℃, and reaction time is 3 minutes, and the results are shown in Table 2. Compared with Comparative Example 1, when a similar desulfurization rate is achieved, the impingement flow reactor needs a shorter reaction time and a lower reaction temperature. And compared with Comparative Example 1, the diesel yield increased by 0.1 wt%.
Embodiment 5
[0042] Embodiment 5 is by embodiment 1 process, and reaction temperature is 70 ℃, and reaction time is 10 minutes, and hydrogen peroxide addition is 2.5 times of theoretical requirement, and the results are shown in Table 2. Compared with Comparative Example 1, to achieve similar desulfurization rate, impinging flow reactor requires less oxidant amount and lower reaction temperature.
PUM
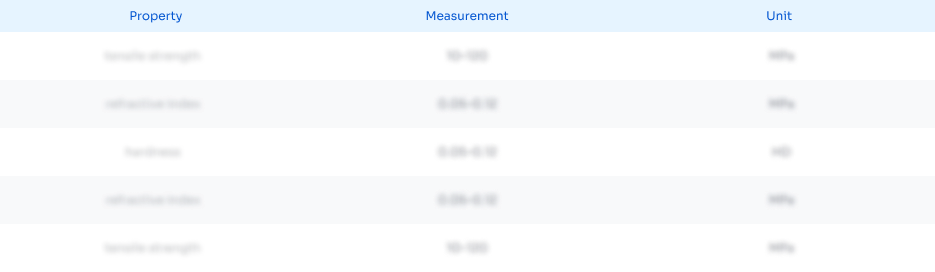
Abstract
Description
Claims
Application Information

- R&D
- Intellectual Property
- Life Sciences
- Materials
- Tech Scout
- Unparalleled Data Quality
- Higher Quality Content
- 60% Fewer Hallucinations
Browse by: Latest US Patents, China's latest patents, Technical Efficacy Thesaurus, Application Domain, Technology Topic, Popular Technical Reports.
© 2025 PatSnap. All rights reserved.Legal|Privacy policy|Modern Slavery Act Transparency Statement|Sitemap|About US| Contact US: help@patsnap.com