Improving Throughput Of Check Valves
Check Valve Technology Background And Goals
Key challenges to be addressed include factors that restrict flow rates, such as valve design, material selection, and operational conditions. Additionally, the analysis should highlight the main technical hurdles hindering higher throughput, such as pressure drop, cavitation, and wear resistance issues. By thoroughly examining the current technological landscape, potential avenues for innovation and breakthrough solutions can be identified.
Check Valve Market Demand Analysis
- Market Size and Growth
The global check valve market is expected to witness significant growth, driven by increasing demand from industries like oil and gas, chemical processing, and water treatment. Factors such as infrastructure development, urbanization, and the need for efficient fluid control systems contribute to market expansion. - Industry Trends
Key trends shaping the check valve market include the adoption of advanced materials for improved durability and corrosion resistance, the demand for compact and lightweight designs, and the integration of smart technologies for remote monitoring and predictive maintenance. - Application Sectors
Check valves find widespread applications across various sectors, including:- Oil and gas: Used in pipelines, refineries, and offshore platforms
- Chemical processing: Employed in chemical plants and processing facilities
- Water and wastewater treatment: Essential for controlling fluid flow in treatment systems
- Power generation: Utilized in power plants and energy facilities
- Regional Dynamics
The Asia-Pacific region is expected to be a significant market for check valves, driven by rapid industrialization and infrastructure development in countries like China and India. North America and Europe also hold substantial market shares due to established industries and stringent regulations.
Check Valve Technology Status And Challenges
- Valve Design Limitations
Current valve designs face challenges in achieving high flow rates due to restrictions in the flow path and turbulence caused by abrupt changes in flow direction. - Material Constraints
The materials used in valve construction can limit their performance, with factors like corrosion resistance, strength, and compatibility with the fluid medium posing challenges. - Scaling and Fouling
Buildup of deposits or scale on valve surfaces can reduce the effective flow area, leading to decreased throughput over time. - Cavitation and Erosion
High-velocity fluid flow can cause cavitation and erosion of valve components, compromising their integrity and reducing service life. - Actuation and Control Issues
Precise control and actuation of valve opening and closing can be challenging, especially in high-flow or high-pressure applications.
Check Valve Technology Evolution Path
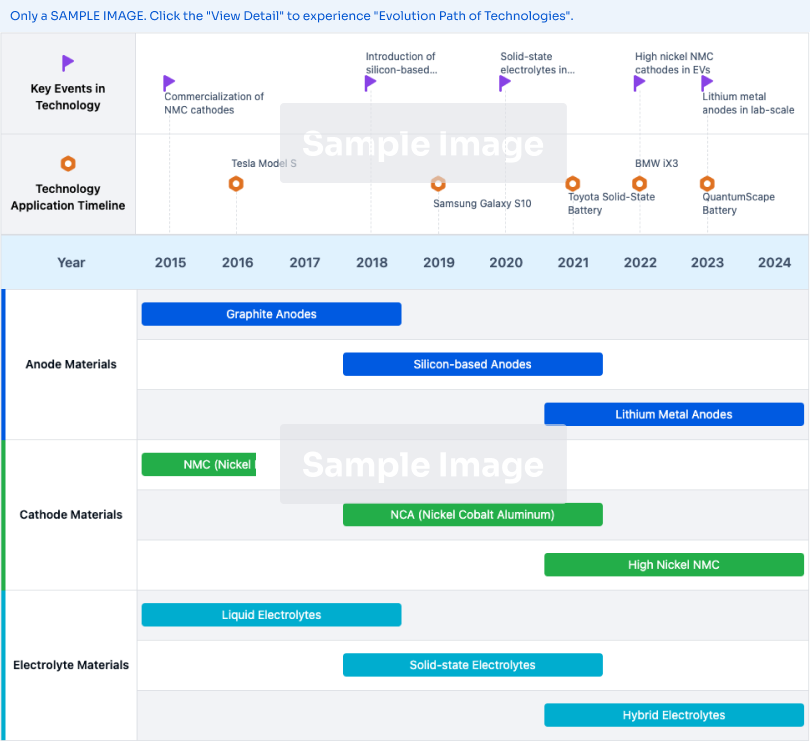
Check Valve Current Technical Solutions
01 Structure and Components
The search results cover various aspects of check valve structure and components, such as valve bodies, valve seats, valve discs or balls, and sealing mechanisms. These components play a crucial role in controlling the flow direction and preventing backflow in check valves.- Check Valve Structure and Components: The search results cover various aspects of check valve structure and components, such as valve bodies, valve seats, valve discs or balls, and sealing mechanisms. These components play a crucial role in controlling the flow direction and preventing backflow in check valves.
- Applications and Industries: The search results discuss the use of check valves in various applications and industries, such as fluid handling systems, pipelines, pumps, and process equipment. Check valves are essential for ensuring proper flow direction and preventing backflow in these applications.
- Performance and Flow Characteristics: The search results cover aspects related to the performance and flow characteristics of check valves, such as flow rates, pressure drop, leakage prevention, and cracking pressure. These factors are crucial for ensuring efficient and reliable operation of check valves.
- Materials and Manufacturing: The search results discuss the materials used in check valve construction, such as metals, plastics, and composites, as well as manufacturing processes like casting, forging, and machining. The choice of materials and manufacturing methods affects the performance and durability of check valves.
- Design and Optimization: The search results cover various aspects of check valve design and optimization, such as valve sizing, flow path optimization, noise reduction, and weight reduction. These design considerations aim to improve the overall performance and efficiency of check valves.
02 Applications and Installation
The search results discuss different applications and installation methods for check valves, such as in fluid systems, pipelines, and various industries. Proper installation and positioning of check valves are essential for their effective operation and preventing backflow.03 Flow Control and Performance
The search results cover aspects related to the flow control and performance of check valves, including flow rates, pressure drop, and throughput. Optimizing these factors is crucial for efficient fluid flow and preventing backflow in various systems.04 Materials and Manufacturing
The search results discuss the materials used in check valve construction, such as metals, plastics, and composites, as well as manufacturing processes like casting, machining, and assembly. Material selection and manufacturing methods impact the durability, performance, and cost of check valves.05 Maintenance and Testing
The search results cover aspects related to the maintenance and testing of check valves, including inspection, repair, and performance evaluation methods. Regular maintenance and testing ensure the proper functioning and reliability of check valves in various applications.
Check Valve Technology Main Player Analysis
Wapro AB
Eaton Corp.
Check Valve Key Technology Interpretation
- The valve member has a convex-curved contact surface, which improves sealing performance.
- The valve member is pretensioned against the valve seat to seal the passage when not in use, preventing backflow.
- The check valve is designed specifically for processing cellulose pulp, addressing the unique challenges of this application.
Check Valve Throughput Improvement Economic Analysis
Check Valve Throughput Improvement Policy And Regulatory Impact
This section examines the policy and regulatory landscape surrounding check valve throughput improvement, aiming to provide insights for informed decision-making. The regulatory framework governing check valve design and performance varies across industries and regions. Stringent standards and guidelines are in place to ensure safety, reliability, and compliance with environmental regulations. Authorities such as the American Society of Mechanical Engineers (ASME) and the International Organization for Standardization (ISO) play a pivotal role in establishing and updating these regulations. Additionally, industry-specific regulations, such as those set by the Environmental Protection Agency (EPA) for the oil and gas sector, or the Food and Drug Administration (FDA) for the pharmaceutical and medical device industries, impose strict requirements on check valve performance and materials. Compliance with these regulations is essential for manufacturers to operate legally and maintain consumer trust.