Advanced Sealing Mechanisms For Check Valves To Improve Sealing Performance
Advanced Sealing Mechanisms For Check Valves: Technology Background And Goals
Particular emphasis will be placed on understanding the current limitations and challenges faced by existing sealing solutions. This entails a thorough assessment of the technical hurdles, constraints, and geographical factors influencing the distribution and adoption of advanced sealing mechanisms. By identifying these obstacles, the report aims to pave the way for innovative approaches and potential breakthroughs in sealing technology.
Check Valve Market Demand Analysis
- Growing Demand for Check Valves Check valves are essential components in various industries, including water and wastewater treatment, oil and gas, chemical processing, and power generation. The demand for check valves is driven by the need for reliable and efficient fluid control systems.
- Market Expansion Across Industries The check valve market is expected to witness significant growth due to the increasing adoption of these valves in diverse industries. The expansion of infrastructure projects, the need for efficient fluid management, and the emphasis on safety and reliability are driving market growth.
- Replacement and Maintenance Needs The replacement and maintenance of existing check valves contribute to the market demand. As check valves age or experience wear and tear, they need to be replaced or serviced to ensure proper functioning and prevent leakage or failure.
- Regulatory Compliance and Safety Standards Stringent regulations and safety standards related to fluid handling systems are driving the demand for high-quality and reliable check valves. Industries must comply with these regulations to ensure safe and efficient operations.
Advanced Sealing Mechanisms For Check Valves: Technology Status And Challenges
- Sealing Challenges Check valves face sealing issues due to high pressures, temperature fluctuations, and corrosive media. Leakage can occur due to wear, deformation, or improper seating.
- Material Limitations Conventional sealing materials like elastomers and metals have limitations in terms of chemical resistance, temperature range, and wear resistance.
- Design Constraints Compact valve designs and complex geometries pose challenges in achieving effective sealing while maintaining flow efficiency.
- Maintenance Requirements Frequent maintenance is often required to replace worn-out seals, leading to downtime and increased operational costs.
Advanced Sealing Mechanisms For Check Valves: Technology Evolution Path
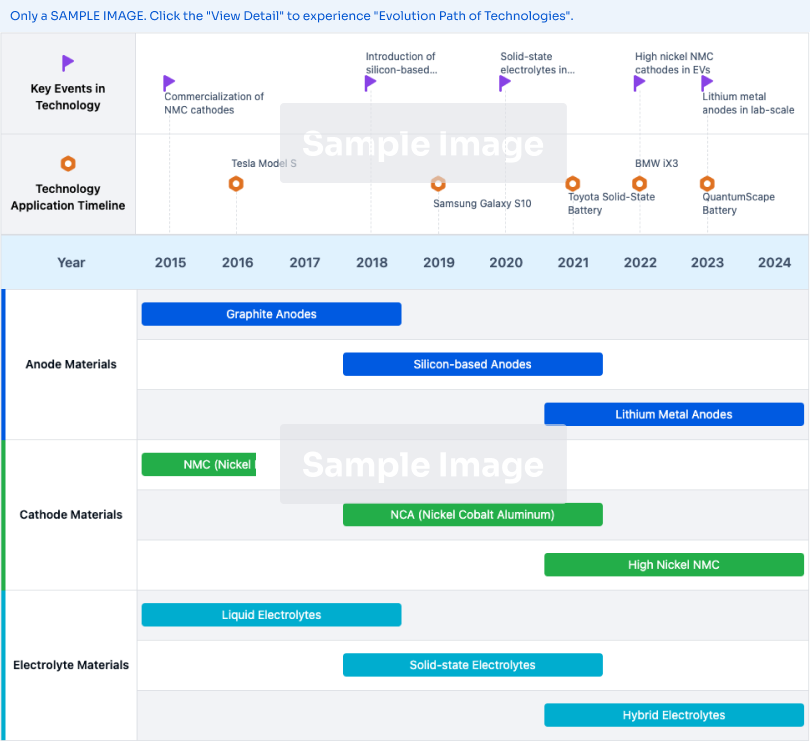
Advanced Sealing Mechanisms For Check Valves: Current Technical Solutions
01 Sealing Structure
The sealing structure, such as resilient sealing members, metal-to-metal sealing surfaces, or a combination, plays a crucial role in ensuring proper sealing and preventing leakage.- Sealing Structure: The sealing structure, including sealing surfaces, sealing members (gaskets, O-rings), and sealing mechanisms, influences the sealing performance of check valves. Optimizing these components can improve sealing effectiveness.
- Materials and Coatings: Selecting suitable materials and coatings for the valve body, sealing components, and sealing surfaces that are compatible with the fluid and resistant to wear and corrosion can enhance sealing capabilities.
- Sealing Force and Pressure: Proper design and selection of components to withstand and maintain sealing under various pressure conditions are crucial for effective sealing performance.
- Sealing Surface Finish and Geometry: Optimizing factors like surface roughness, flatness, and sealing interface geometry can improve sealing performance by reducing leakage paths.
- Maintenance and Monitoring: Regular maintenance, inspection, and monitoring of sealing components can help identify and address potential sealing issues, ensuring optimal sealing performance over time.
02 Materials and Coatings
Certain materials and coatings can enhance sealing properties, improve wear resistance, and prevent corrosion or fouling, maintaining effective sealing over time.03 Design and Configuration
Factors like valve geometry, flow path design, and the arrangement of sealing components can impact the sealing effectiveness and prevent leakage under various operating conditions.04 Sealing Mechanisms
Different sealing mechanisms, such as spring-loaded sealing elements, pressure-assisted sealing, or specialized sealing geometries, can be employed to ensure proper sealing under various flow conditions.05 Maintenance and Testing
Regular inspections, cleaning, component replacement, leak testing, and performance verification can help maintain the sealing performance of check valves over time.
Advanced Sealing Mechanisms For Check Valves: Main Player Analysis
Halliburton Energy Services, Inc.
Neway Valve (Suzhou) Co., Ltd.
Advanced Sealing Mechanisms For Check Valves: Key Technology Interpretation
- A lip seal for a check ring of a check valve for a metal injection machine, with a groove interior of a circumferential surface of the ring that engages with a surface of the valve to block flow of injection material into a melt passageway.
- A check valve with a groove formed in a forward face of the ring portion that receives melt to force an outer circumferential portion of the ring in a radial direction to provide a seal between the ring portion and a wall in the machine.
- The use of a lip seal design with a groove and circumferential sealing surface, specifically tailored for metal injection molding and die casting applications.
Advanced Sealing Mechanisms For Check Valves: Potential Innovation Direction
- Check Valves with Advanced Sealing Mechanisms Using Shape Memory Alloys
- Check Valves with Self-Cleaning Capabilities Using Superhydrophobic Coatings
- Check Valves with Adaptive Sealing Using Soft Robotics and Flexible Materials