Check Valves With Optimized Sealing Geometries For Improved Sealing Performance
Check Valve Technology Background And Goals
The analysis will cover the geographical distribution of relevant research and development activities, as well as the major players involved in this field. It will also identify the core patents and technical literature that underpin innovative approaches to optimizing sealing geometries for enhanced sealing capabilities.
Check Valve Market Demand Analysis
- Market Size and Growth
Provide an overview of the current market size for check valves, highlighting key application areas and industries. Analyze historical market data to identify growth trends and project future market potential. - Regional Demand Analysis
Examine the regional distribution of demand for check valves, identifying major markets and growth hotspots. Discuss factors influencing regional demand, such as industrial development, infrastructure projects, and regulatory environments. - Application Segmentation
Segment the check valve market based on various applications, such as oil and gas, water and wastewater treatment, chemical processing, and power generation. Analyze the specific requirements and demand drivers for each application segment. - End-User Analysis
Identify the key end-user industries for check valves, including their unique needs and preferences. Evaluate the impact of factors like cost, performance, and reliability on end-user demand. - Emerging Trends and Opportunities
Highlight emerging trends and opportunities in the check valve market, such as the demand for high-performance materials, compact designs, or specialized applications. Discuss how these trends may shape future market demand.
Check Valve Technology Status And Challenges
- Sealing Challenges Conventional check valves often face issues like leakage, wear, and reduced sealing performance over time, leading to inefficiencies and potential safety hazards.
- Geometric Optimization Optimizing the sealing geometry, such as the shape and surface finish of the valve seat and disc, can enhance sealing performance and reduce wear.
- Materials and Coatings Advanced materials and coatings can improve durability, corrosion resistance, and sealing properties, addressing challenges in harsh environments.
- Computational Modeling Computational fluid dynamics (CFD) and finite element analysis (FEA) enable simulations to optimize sealing geometries and predict performance.
Check Valve Technology Evolution Path
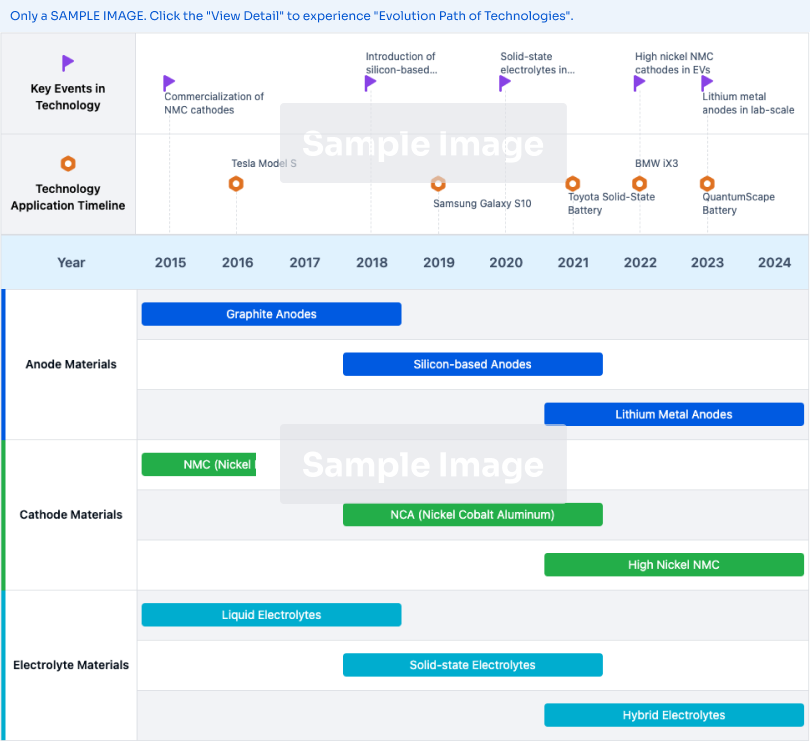
Check Valve Current Technical Solutions
01 Check Valve Sealing Structure
Optimizing the sealing structure, using specialized sealing materials, incorporating sealing elements, or designing unique sealing geometries can enhance the sealing capability and prevent leakage in check valves.- Check Valve Sealing Structure: Optimizing the design of sealing surfaces, sealing members (e.g., O-rings, gaskets), and sealing mechanisms can improve the sealing effectiveness of check valves.
- Check Valve Materials and Coatings: Selecting suitable materials for valve bodies, sealing surfaces, and sealing members, as well as applying coatings or surface treatments, can enhance sealing performance, wear resistance, and corrosion resistance.
- Check Valve Design and Configuration: Optimizing factors like valve geometry, flow path, and sealing force can lead to improved sealing capabilities in check valves.
- Check Valve Sealing Mechanisms and Principles: Understanding and optimizing sealing mechanisms and principles, such as mechanical sealing, fluid sealing, or a combination, can enhance the sealing performance of check valves.
- Check Valve Testing and Evaluation Methods: Developing and implementing appropriate testing procedures, such as leak testing, pressure testing, and flow testing, can help identify and address sealing issues in check valves.
02 Check Valve Sealing Materials
Employing specialized sealing materials with desirable properties like chemical resistance, temperature tolerance, and low friction can improve sealing effectiveness and durability in check valves.03 Check Valve Sealing Mechanisms
Incorporating sealing mechanisms like spring-loaded sealing elements, pressure-assisted sealing, or specialized valve seat designs can enhance sealing performance under different operating conditions.04 Check Valve Sealing Surface Treatments
Surface treatments like coatings, polishing, or texturing techniques applied to sealing surfaces can improve sealing contact, reduce friction, and increase wear resistance in check valves.05 Check Valve Sealing Assembly Designs
The overall design of the check valve sealing assembly, including the arrangement of sealing components, multiple sealing stages, or additional sealing elements, can impact the overall sealing capability.
Check Valve Main Player Analysis
Fisher Controls International LLC
Schlumberger Technologies, Inc.
Check Valve Key Technology Interpretation
- The sealing member has a concave hemispherical shape that fits tightly with the housing's annular seat, providing an effective seal when in the closed position.
- The sealing member has an elastomeric flange that forms a clearance fit or interference fit with the housing, enhancing the sealing capability.
- The housing is made up of two pieces that are joined together, allowing for easier assembly and maintenance.
Check Valve Potential Innovation Direction
- Check Valves with Optimized Sealing Geometries for Improved Sealing Performance
- Check Valves with Integrated Condition Monitoring and Predictive Maintenance
- Check Valves with Advanced Flow Control and Energy Harvesting Capabilities
Environmental Impact Considerations of Check Valves With Optimized Sealing Geometries
Environmental considerations are crucial when optimizing sealing geometries for check valves. Proper material selection and disposal methods are vital to minimize environmental impact. Recyclable and biodegradable materials should be prioritized. Additionally, optimized geometries can reduce leakage and emissions, lowering the overall environmental footprint. Life cycle assessments should be conducted to evaluate the environmental impact throughout the valve's lifespan, from material sourcing to disposal. Adherence to relevant environmental regulations and standards is essential for responsible manufacturing and operation.