Check Valves With Additive Manufacturing For Optimized Internal Geometries
Technology Background And Goals
Key areas of focus include designing and fabricating check valve components with tailored internal features, such as streamlined flow channels, integrated guides, and optimized sealing surfaces. The research aims to investigate the impact of these optimized geometries on factors like pressure drop, flow characteristics, and valve reliability, ultimately leading to improved energy efficiency and extended service life.
Check Valves Market Demand Analysis
- Market Size and Growth
Provide an overview of the current market size for check valves, highlighting key application areas and industries. Analyze historical market growth trends and forecast future growth potential, considering factors like industrial expansion, infrastructure development, and regulatory changes. - Regional Market Analysis
Examine the regional distribution of the check valve market, identifying major manufacturing hubs and high-demand regions. Discuss regional variations in market dynamics, such as pricing, competition, and regulatory environments. - Application Segmentation
Segment the check valve market based on various applications, such as oil and gas, chemical processing, water and wastewater treatment, power generation, and others. Analyze the specific requirements and demand drivers for each application segment. - Emerging Trends and Opportunities
Identify emerging trends shaping the check valve market, such as the adoption of additive manufacturing, the demand for compact and lightweight designs, and the need for improved performance and reliability. Discuss potential opportunities arising from these trends. - Challenges and Constraints
Highlight the key challenges and constraints faced by the check valve market, including material limitations, manufacturing complexities, regulatory hurdles, and competition from alternative technologies. Discuss strategies to mitigate these challenges.
Technology Status And Challenges
- Additive Manufacturing Advantages
Additive manufacturing (AM) enables the production of complex internal geometries that are difficult or impossible to achieve with traditional manufacturing methods, allowing for optimized flow paths and improved performance. - Design Freedom
AM's layer-by-layer fabrication process allows for the creation of intricate internal structures, such as lattices, channels, and cavities, without the constraints of conventional manufacturing techniques. - Material Versatility
AM can be used with a wide range of materials, including metals, polymers, and composites, enabling the production of check valves with tailored properties and characteristics. - Customization and Optimization
AM facilitates the customization and optimization of check valve designs for specific applications, enabling improved flow characteristics, reduced pressure drop, and enhanced reliability. - Lightweight Structures
The ability to create complex internal geometries with AM allows for the production of lightweight check valves with optimized strength-to-weight ratios, which is particularly beneficial in applications where weight is a critical factor.
Technology Evolution Path
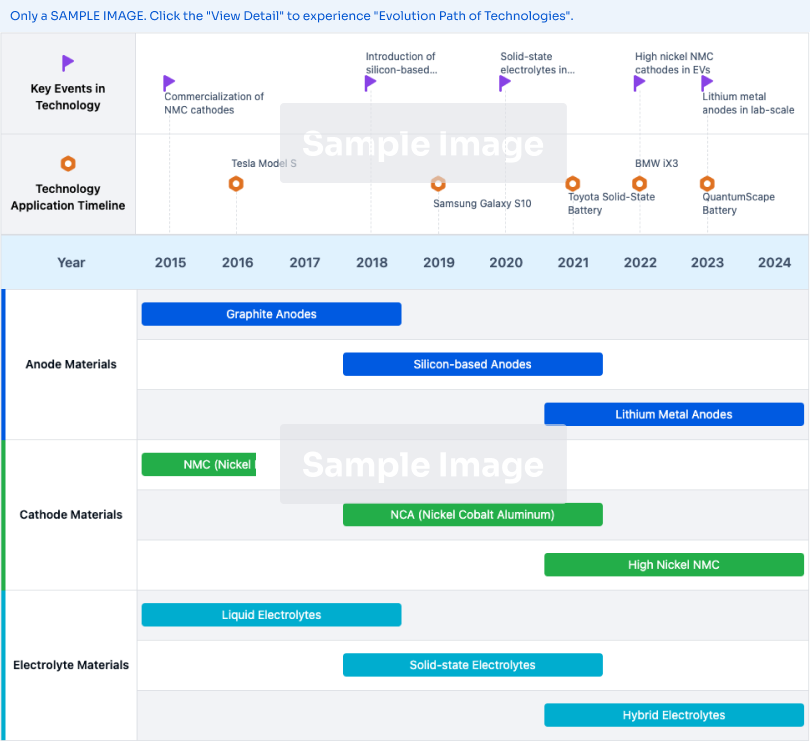
Current Technical Solutions
01 Tilting Disc Design
The internal geometry features a pivotally mounted tilting disc that opens or closes the valve, allowing efficient flow control and minimizing pressure drop.- Tilting Disc Design: The internal geometry features a tilting disc pivotally mounted within the valve body, allowing efficient flow control and minimizing pressure drop.
- Guided Piston Arrangement: The internal geometry incorporates a guided piston or plunger within the valve body, providing precise flow control and handling high pressures.
- Spring-Loaded Valve Element: The internal geometry includes a spring-loaded valve element, such as a ball or poppet, biased against a valve seat for quick response to pressure changes.
- Multiple Flow Paths: The internal geometry incorporates multiple flow paths or channels, offering flexibility in controlling flow direction or rate for various applications.
- Integrated Flow Control Features: The internal geometry includes integrated features like diffusers, vortex generators, or flow straighteners for improved flow characteristics and reduced turbulence or cavitation.
02 Guided Piston Design
The internal geometry incorporates a guided piston within a cylinder for precise flow regulation and preventing backflow.03 Spring-Loaded Valve Element
The internal geometry includes a spring-loaded valve element, like a ball or disc, held in place by a spring for reliable opening and closing.04 Multiple Valve Elements
The internal geometry features multiple valve elements arranged in series or parallel, providing redundancy and improved flow control capabilities.05 Integrated Flow Conditioning
The internal geometry incorporates flow conditioning features, such as diffusers or straightening vanes, to optimize flow patterns and reduce turbulence.
Technology Main Player Analysis
The competitive landscape for check valves with additive manufacturing for optimized internal geometries is evolving rapidly, driven by advancements in additive manufacturing technologies. The market is expanding as more sectors recognize the benefits of optimized internal geometries for improved performance and efficiency.
Collins Engine Nozzles, Inc.
Robert Bosch GmbH
Key Technology Interpretation
- The use of a tilted orientation during the additive manufacturing process. this allows for the manufacturing of complex fluid pump designs that would be difficult or impossible to manufacture using traditional methods.
Check Valves Potential Innovation Direction
- Check Valves with Optimized Internal Geometries through Additive Manufacturing
- Check Valves with Integrated Sensors and Monitoring Systems
- Check Valves with Advanced Materials and Surface Coatings
Economic Analysis
Additive manufacturing (AM) allows for the fabrication of complex geometries that are difficult or impossible to achieve through traditional subtractive manufacturing methods. This flexibility presents an opportunity for optimizing the internal geometries of check valves, potentially leading to improved performance, increased efficiency, and reduced material consumption.
The economic impact of optimizing check valve geometries through AM can be significant. By enabling the production of intricate internal structures, AM can enhance fluid dynamics and reduce pressure losses, which in turn can lead to energy savings in various fluid handling systems. Additionally, the ability to consolidate multiple components into a single printed part can streamline manufacturing processes, reduce assembly costs, and minimize potential failure points.
Furthermore, AM's ability to produce complex shapes with minimal material waste could result in substantial material cost savings, particularly when working with expensive alloys or specialized materials required for specific applications. This advantage becomes even more pronounced when dealing with small production runs or customized valve designs, where traditional manufacturing methods may not be economically viable.
It is crucial to consider the potential capital investment required for implementing AM technologies, along with the associated costs of materials, post-processing, and quality control measures. However, these upfront costs may be offset by long-term savings resulting from improved efficiency, reduced energy consumption, and streamlined manufacturing processes.
Moreover, the ability to rapidly iterate and optimize check valve designs through AM could significantly shorten product development cycles, enabling faster time-to-market and improved competitiveness. This agility can be particularly advantageous in industries that require frequent design iterations or customized solutions.
Overall, the economic benefits of optimizing check valve internal geometries through AM stem from improved performance, increased efficiency, material savings, streamlined manufacturing processes, and accelerated product development cycles. A comprehensive cost-benefit analysis considering the specific application, production volumes, and operational requirements would be necessary to quantify the potential economic impact and justify the adoption of this technology.
Policy And Regulatory Impact
The regulatory impact of additive manufacturing (AM) for optimized internal geometries of check valves is a complex and multi-faceted issue. The adoption of this technology is influenced by various regulatory frameworks, industry standards, and safety considerations.
Regulatory bodies such as the U.S. Food and Drug Administration (FDA), the European Medicines Agency (EMA), and the International Organization for Standardization (ISO) play a crucial role in establishing guidelines and requirements for the use of AM in critical applications like check valves. These regulations cover aspects such as material selection, manufacturing processes, quality control, and testing protocols to ensure the safety and reliability of the final products.
One of the primary concerns for regulatory agencies is the consistency and reproducibility of AM processes. Traditional manufacturing methods have well-established quality control measures, but AM introduces new variables that need to be carefully monitored and controlled. Regulatory agencies may require extensive testing and validation to demonstrate that the optimized internal geometries produced through AM meet the necessary performance criteria and do not compromise the functionality or safety of the check valves.
Additionally, the regulatory landscape may vary across different industries and regions, creating challenges for companies operating in multiple markets. Harmonization of standards and regulations is an ongoing effort to facilitate the adoption of AM technologies while ensuring consistent levels of safety and quality.
As AM technologies continue to evolve, regulatory bodies will need to adapt their guidelines and frameworks to keep pace with the rapid advancements in this field. This may involve collaborating with industry stakeholders, research institutions, and international organizations to develop comprehensive standards and best practices for the application of AM in critical components like check valves.