System and method for measuring pressure applied by a piezo-electric pump
a piezo-electric pump and piezoelectric technology, applied in the direction of machines/engines, liquid fuel engines, positive displacement liquid engines, etc., can solve the problem that high amplitude acoustic resonance has not been employed in disc-shaped cavities, and achieve the effect of effective and economical control of the operation of the disc pump and reducing pressur
- Summary
- Abstract
- Description
- Claims
- Application Information
AI Technical Summary
Benefits of technology
Problems solved by technology
Method used
Image
Examples
Embodiment Construction
[0028]FIGS. 1A and 1B are illustrations of a cross-section view of an illustrative disc pump 100 in accordance with illustrative embodiments. As shown, the disc pump 100 may include a pump housing 102 having a substantially elliptical shape including a elliptical wall 101 closed at one end by a base wall 103 and mounted at the other end by legs 105 attached to a circuit board 108 or other substrate to support the pump housing 102. The elliptical wall 101, the legs 105, and base wall 103 together form the pump housing 102. The pump 100 further comprises a pair of disc-shaped interior plates 114, 115 supported within the pump 100 by a ring-shaped skirt 130 affixed to the elliptical wall 101 of the pump body. The internal surfaces of the elliptical wall 101, the base wall 103, the interior plate 114, and the ring-shaped skirt 130 form a cavity 116 within the pump 100. The internal surfaces of the cavity 116 comprise a side wall 118 which is a first portion of the inside surface of the ...
PUM
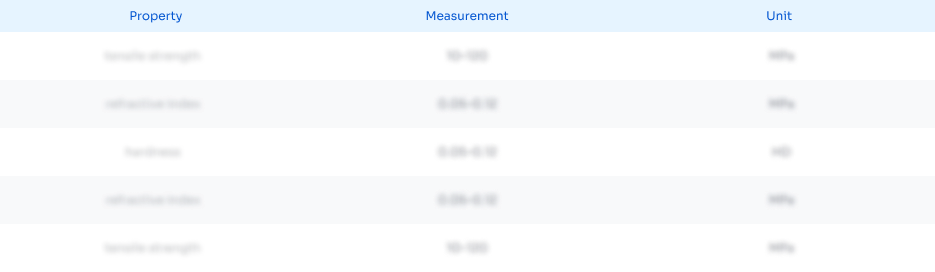
Abstract
Description
Claims
Application Information

- R&D
- Intellectual Property
- Life Sciences
- Materials
- Tech Scout
- Unparalleled Data Quality
- Higher Quality Content
- 60% Fewer Hallucinations
Browse by: Latest US Patents, China's latest patents, Technical Efficacy Thesaurus, Application Domain, Technology Topic, Popular Technical Reports.
© 2025 PatSnap. All rights reserved.Legal|Privacy policy|Modern Slavery Act Transparency Statement|Sitemap|About US| Contact US: help@patsnap.com