Process for manufacturing emulsified fuels by using oily water
a technology of emulsified fuels and oil, which is applied in the direction of fuels, liquid carbonaceous fuels, petroleum industry, etc., can solve the problems of increasing fuel consumption, causing environmental pollution, and a large amount of unburned carbon particulates, etc., to achieve easy preparation, low cost, and the effect of enhancing combustion efficiency
- Summary
- Abstract
- Description
- Claims
- Application Information
AI Technical Summary
Benefits of technology
Problems solved by technology
Method used
Image
Examples
Embodiment Construction
[0037]As shown in FIG. 1, a preferred embodiment of a process for manufacturing emulsified fuels by using “oily water” in the present invention is processed with the following steps: (a) preparing the “oily water” that has 0.02˜30% (w / w) of combustible fuel dissolved in water and blended with surfactants (or called as emulsifiers) by 0.01˜3% (w / w); (b) mixing the “oily water” an d the surfactants t h at was finished by step (a) with 60˜95% (w / w) of conventional heavy fuel oil or with 75˜98% (w / w) of conventional diesel, respectively; (c) mixing the two mixtures, respectively, that was finished by step (b) further by using homogenizer to become an “oily water emulsified heavy oil”, denoted as OWEH, and an “oily water emulsified diesel”, denoted as OWED, respectively.
[0038]As the “oily water” is a necessary raw material in the present invention, it therefore must be obtained before proceeding with any further manufacturing step. The “oily water” is gained via plural ways: (1) adding 0...
PUM
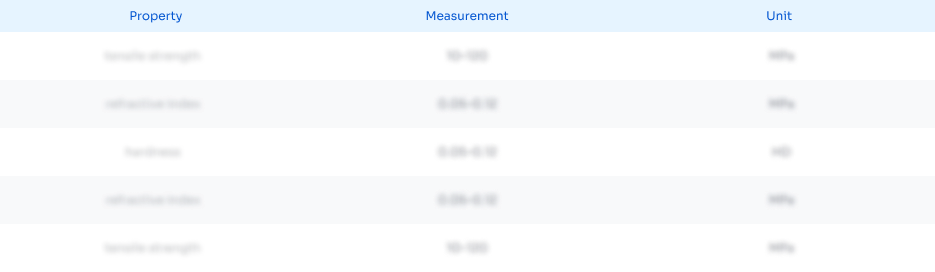
Abstract
Description
Claims
Application Information

- R&D Engineer
- R&D Manager
- IP Professional
- Industry Leading Data Capabilities
- Powerful AI technology
- Patent DNA Extraction
Browse by: Latest US Patents, China's latest patents, Technical Efficacy Thesaurus, Application Domain, Technology Topic, Popular Technical Reports.
© 2024 PatSnap. All rights reserved.Legal|Privacy policy|Modern Slavery Act Transparency Statement|Sitemap|About US| Contact US: help@patsnap.com