Precision measuring collision avoidance system
a collision avoidance and precision technology, applied in the field of sensor-based systems, can solve the problems of increasing the number of accidents, driving only in one spot at any one time, and traffic congestion on the road becoming more and more congested
- Summary
- Abstract
- Description
- Claims
- Application Information
AI Technical Summary
Benefits of technology
Problems solved by technology
Method used
Image
Examples
example
Deepest Hole
Suppose the following agreement matrix was generated with MST (rows) and sensor (columns) tracks. All possible standard differences between the MST and sensor data are calculated and placed into the matrix. For this example it will be assumed that all standard differences fall below the limiting value (step 1). Since this matdx contains more rows than columns, the matrix is transposed (step 2). Sensor DetectionsMSTTracks 12311.72.02.721.82.55.433.12.71.542.36.21.9⇒transpose⇒MST Tracks SensorDetections 123411.71.83.12.322.02.52.76.232.75.41.51.9
The difference between the minimum and next minimum values for each row is then calculated (step 5).
Row 1Row 2Row 3(next min) − (min) A:0.10.50.4
The largest value found (i.e. deepest hole) is 0.5 corresponding to Row 2 or Sensor Detection 2. This row is then examined to find the corresponding column (MST track) which has the minimum standard difference. The minimum is 2.0 corresponding to column 1. The smalles...
PUM
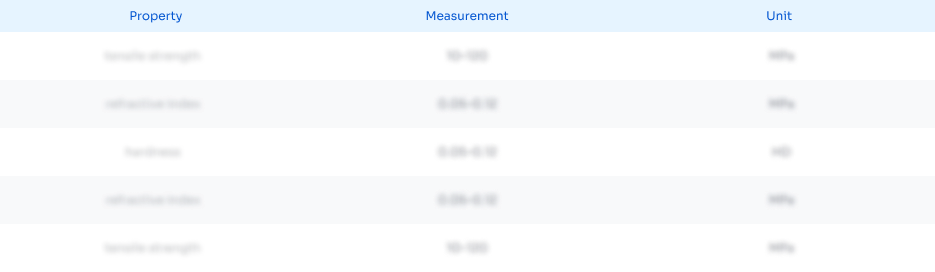
Abstract
Description
Claims
Application Information

- R&D
- Intellectual Property
- Life Sciences
- Materials
- Tech Scout
- Unparalleled Data Quality
- Higher Quality Content
- 60% Fewer Hallucinations
Browse by: Latest US Patents, China's latest patents, Technical Efficacy Thesaurus, Application Domain, Technology Topic, Popular Technical Reports.
© 2025 PatSnap. All rights reserved.Legal|Privacy policy|Modern Slavery Act Transparency Statement|Sitemap|About US| Contact US: help@patsnap.com