Integrated, proportionally controlled, and naturally compliant universal joint actuator with controllable stiffness
a universal joint actuator technology, applied in the field of pneumatically operated actuation systems, can solve the problems of increasing the overall size of the vehicle, inability to successfully and reliably traverse, and useless robot devices, and achieve the effect of minimizing airflow and stiffness control
- Summary
- Abstract
- Description
- Claims
- Application Information
AI Technical Summary
Benefits of technology
Problems solved by technology
Method used
Image
Examples
Embodiment Construction
The following description of the preferred embodiment is merely exemplary in nature and is in no way intended to limit the invention, its application, or uses. That is, it should be understood that although the present invention is discussed in connection with robotic devices, the present invention might find utility in a wide variety of applications.
Briefly, by way of background, there are a number of desirable design criteria that ideally would be met in a commercially viable serpentine robot. Serpentine robots are typically relatively long compared to their diameter, so that their lead segments can reach up and over a high step while still being able to fit through small openings. Because of this geometric constraint, as well as other unique characteristics of serpentine robots, the following requirements can be derived (in decreasing order of importance).
It is primarily desirable that a serpentine robot be able to compliantly conform to terrain, such that the maximum number...
PUM
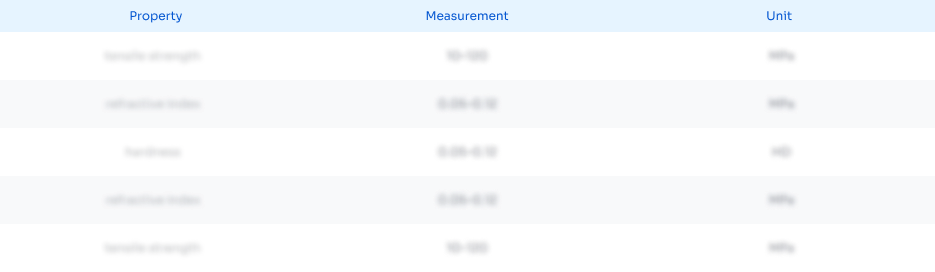
Abstract
Description
Claims
Application Information

- R&D
- Intellectual Property
- Life Sciences
- Materials
- Tech Scout
- Unparalleled Data Quality
- Higher Quality Content
- 60% Fewer Hallucinations
Browse by: Latest US Patents, China's latest patents, Technical Efficacy Thesaurus, Application Domain, Technology Topic, Popular Technical Reports.
© 2025 PatSnap. All rights reserved.Legal|Privacy policy|Modern Slavery Act Transparency Statement|Sitemap|About US| Contact US: help@patsnap.com