Caisson 3D scene rebuilding and excavator collision avoidance system based on laser scanning
A laser scanning, three-dimensional scene technology, applied in caisson, earthmoving machine/shovel, construction, etc., can solve the problem of caisson excavator operator's poor sense of presence, difficulty in understanding the excavator caisson environment, and inability to display the inside of the caisson. Three-dimensional topography and other problems, to avoid collision of excavators, increase production efficiency, and achieve the effect of safe production
- Summary
- Abstract
- Description
- Claims
- Application Information
AI Technical Summary
Problems solved by technology
Method used
Image
Examples
Embodiment Construction
[0015] The system of the present invention will be further described below in conjunction with the accompanying drawings.
[0016] As shown in Figure 1, this embodiment includes four modules: a sensor module, a motion control module, a three-dimensional landform modeling and display module, and an excavator collision avoidance algorithm module. The sensor module includes a laser scanning sensor 7, a laser ranging sensor 10, and an inclination sensor 3. The data collected by these sensors is sent to the three-dimensional landform modeling and display module; the motion control module includes a motion controller 9, a stepper motor 5, and a worm gear reducer. Machine 4, the motion control module controls the laser scanning sensor 7 in the sensor module to rotate around the rotation axis 8 of the reducer, and transmits the angle of rotation to the three-dimensional landform modeling and display module; the three-dimensional landform modeling and display module uses the inclination...
PUM
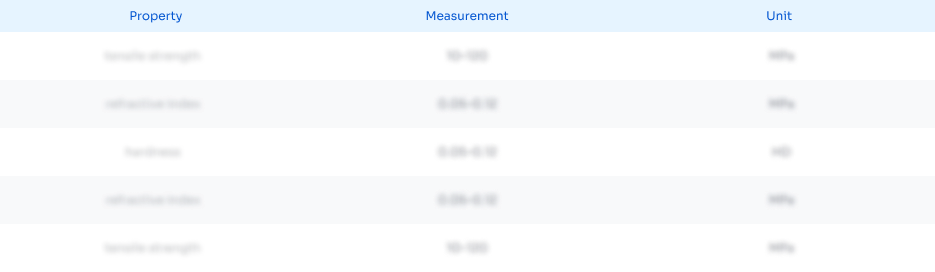
Abstract
Description
Claims
Application Information

- Generate Ideas
- Intellectual Property
- Life Sciences
- Materials
- Tech Scout
- Unparalleled Data Quality
- Higher Quality Content
- 60% Fewer Hallucinations
Browse by: Latest US Patents, China's latest patents, Technical Efficacy Thesaurus, Application Domain, Technology Topic, Popular Technical Reports.
© 2025 PatSnap. All rights reserved.Legal|Privacy policy|Modern Slavery Act Transparency Statement|Sitemap|About US| Contact US: help@patsnap.com