Coating apparatus
A coating device and coating technology, applied to the surface coating liquid device, coating, optics, etc., can solve the problems of easy vibration, uneven coating of alignment film materials, and removal of blades 16, etc., to achieve The effect of reducing the incidence
- Summary
- Abstract
- Description
- Claims
- Application Information
AI Technical Summary
Problems solved by technology
Method used
Image
Examples
Embodiment Construction
[0054] Please refer to FIG. 2A , which is a schematic diagram of a coating device according to a preferred embodiment of the present invention. As shown in FIG. 2A , the coating device 20 includes a rotating shaft 21 , a coating unit 22 , a counterweight unit 23 and a driving unit 24 . The rotating shaft 21 is arranged on a device base frame 25 and can rotate relative to the device base frame 25 . The coating unit 22 is fixed on the rotating shaft 21 and can rotate along with the rotating shaft 21 . The counterweight unit 23 is rotatably disposed on the rotating shaft 21 and is located on two sides of the rotating shaft 21 with the coating unit 22 respectively. The counterweight unit 23 is used to balance the weight of the coating unit 22 . The driving unit 24 is coupled to the rotating shaft 21 to drive the rotating shaft 21 to rotate, thereby adjusting the distance between the coating unit 22 and a printing wheel 26 and adjusting the pressing force of the coating unit 22 on ...
PUM
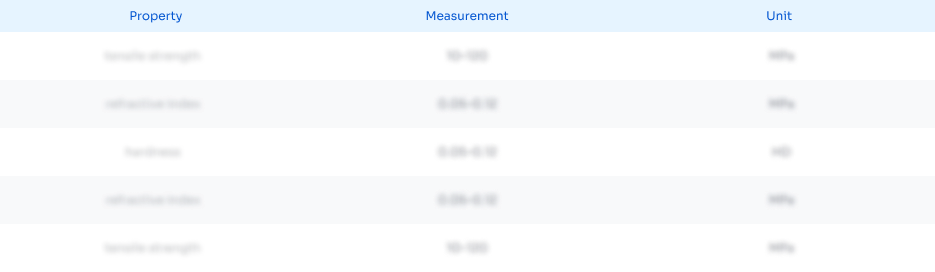
Abstract
Description
Claims
Application Information

- R&D Engineer
- R&D Manager
- IP Professional
- Industry Leading Data Capabilities
- Powerful AI technology
- Patent DNA Extraction
Browse by: Latest US Patents, China's latest patents, Technical Efficacy Thesaurus, Application Domain, Technology Topic, Popular Technical Reports.
© 2024 PatSnap. All rights reserved.Legal|Privacy policy|Modern Slavery Act Transparency Statement|Sitemap|About US| Contact US: help@patsnap.com