Zinc electrolysis direct current coating technology for new anode plate
A technology of anode plate and zinc electrolysis, applied in the direction of electrodes, photographic technology, electrolysis process, etc., can solve the problems of limited production quantity and affecting product quality, achieve the effect of improving production efficiency and ensuring supplementary supply
- Summary
- Abstract
- Description
- Claims
- Application Information
AI Technical Summary
Problems solved by technology
Method used
Image
Examples
Embodiment Construction
[0010] Such as figure 1 As shown, a new anode plate DC electroplating process for zinc electrolysis is specifically as follows: the flat cathode plate 3 and the anode plate 4 to be coated are installed in the coating tank 10, and the cathode plate 3 and the anode plate 4 are evenly distributed in a staggered manner. Conductor 7 (positive pole conductor) leads down positive pole from the anode plate 1 on the electrolytic cell 9 and is connected on the anode bus bar 5 on the coating tank 10, and the anode plate and the anode bus bar adopt an overlapping connection mode, and the conductor 8 ( Negative pole conductor) leads down from the cathode plate 2 on the electrolytic cell 9 and is connected to the cathode plate busbar 6 on the coating tank 10, and the cathode plate and the cathode busbar also adopt an overlapping connection mode to form a whole circuit. The anode plate in the coating tank 10 is used for coating production.
[0011] The distance between the cathode plate 3 a...
PUM
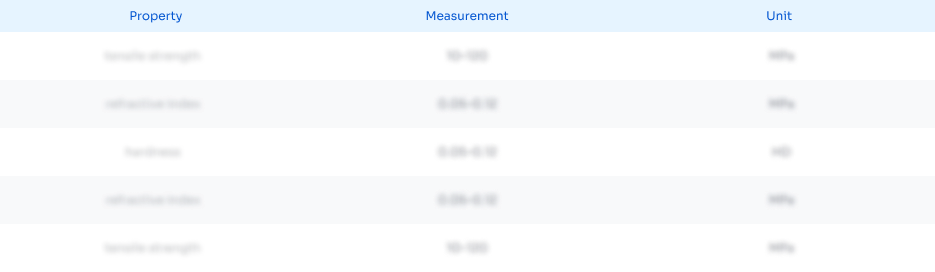
Abstract
Description
Claims
Application Information

- Generate Ideas
- Intellectual Property
- Life Sciences
- Materials
- Tech Scout
- Unparalleled Data Quality
- Higher Quality Content
- 60% Fewer Hallucinations
Browse by: Latest US Patents, China's latest patents, Technical Efficacy Thesaurus, Application Domain, Technology Topic, Popular Technical Reports.
© 2025 PatSnap. All rights reserved.Legal|Privacy policy|Modern Slavery Act Transparency Statement|Sitemap|About US| Contact US: help@patsnap.com