Process for the return extrusion of internal profiles
A technology of inner profile and process, which is applied in the field of inner profile, can solve the problems of incomplete filling and unusability of the profile
- Summary
- Abstract
- Description
- Claims
- Application Information
AI Technical Summary
Problems solved by technology
Method used
Image
Examples
Embodiment Construction
[0021] figure 1 The details of a tube 11 are shown, in which an inner profile is about to be produced. It is also possible to use a substantially uniform closed tubular profile instead of the tube. In this case, the support sleeve and the forming die must be adapted accordingly.
[0022] In FIG. 2, the tube 11 is inserted into a support sleeve 12 in a substantially gap-free manner, and in order to obtain axial support, the two are located on a base plate 13 with a central hole. The base plate 13 directly supports the first tube end 19. The second rear tube end 20 is the free end. At a distance from the support sleeve 12, a coaxially arranged mold 14 with an attached molding mold 15 is provided in order to create an inner profile in the tube 11. On the mold 14, an annular mold 16 is slid, and at its front end, there is an inner groove 17 partially accommodating the molding mold 15.
[0023] In FIG. 3, the forming mold 15 for producing an inner profile 18 has been partially presse...
PUM
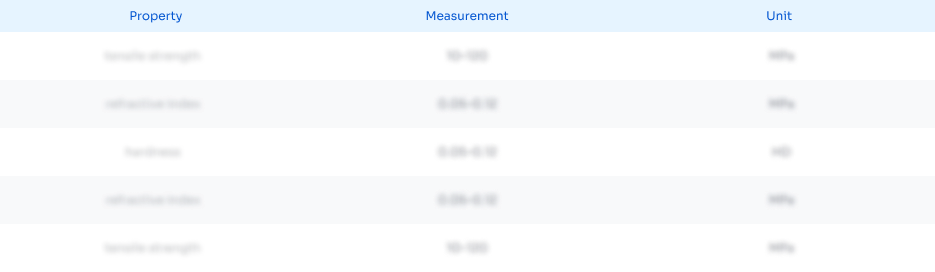
Abstract
Description
Claims
Application Information

- R&D
- Intellectual Property
- Life Sciences
- Materials
- Tech Scout
- Unparalleled Data Quality
- Higher Quality Content
- 60% Fewer Hallucinations
Browse by: Latest US Patents, China's latest patents, Technical Efficacy Thesaurus, Application Domain, Technology Topic, Popular Technical Reports.
© 2025 PatSnap. All rights reserved.Legal|Privacy policy|Modern Slavery Act Transparency Statement|Sitemap|About US| Contact US: help@patsnap.com