Method of obtaining 2-mercaptobenzothiazole
A technology for mercaptobenzothiazole and aniline, which is applied in the field of obtaining 2-mercaptobenzothiazole and can solve the problems of no description, no effect, etc.
- Summary
- Abstract
- Description
- Claims
- Application Information
AI Technical Summary
Problems solved by technology
Method used
Examples
Embodiment 1
[0036] (The aniline filtrate is not recycled)
[0037] 93.13 grams of aniline, 31.42 grams of sulfur and 80.67 grams of carbon disulfide were charged into a 300 ml pressure reactor. Under the conditions customary for this synthesis (220 to 300° C. / 6 to 11.1 MPa), a melt of the crude 2-mercaptobenzothiazole is prepared. After the reaction, the reactor was cooled to 180°C to 200°C, and the contents of the reactor were purged with a nitrogen flow at 200°C to remove volatile components.
[0038] 155 g of purged melt (containing 92.3% of 2-mercaptobenzothiazole, 1.72% of benzothiazole, 2.14% of sulfur and 3.84% of bitumen) and 8.9 g of volatile fraction (aniline and benzothiazole mixture)
[0039] The melt was hot-dissolved in 250 g of aniline, 2-mercaptobenzothiazole was crystallized by cooling, and after filtration and drying, 114.6 g of product were obtained (i.e., a theoretical yield of 68.5 g relative to the aniline charged to the reactor %, the yield relative to the conten...
Embodiment 2
[0040] Embodiment 2 (after reaching steady state repeatedly by part aniline filtrate circulation)
[0041] 100 g of the aniline filtrate from the crystallization step (containing 78% aniline, 9.5% 2-mercaptobenzothiazole) was mixed with 27 g of sulfur, 67 g of carbon disulfide and 9 g of the volatile fraction from the previous melt purge step ( Containing 30% aniline and 65% benzothiazole) were fed together into a 300 ml pressure reactor. Under the conditions customary for this synthesis (220 to 300° C. / 6 to 11.1 MPa), a melt of the crude product is obtained. After the reaction, the reactor was cooled to 180 to 200° C., and the contents of the reactor were purged with nitrogen flow at 200° C. to remove volatile parts.
[0042] Obtained 162.3 g of purged melt containing 91.0% of 2-mercaptobenzothiazole, 2.0% of benzothiazole, 1.5% of sulfur, 0.9% of anilinobenzothiazole, 0.1% of Phenylthiourea, 0.07% of 2-methylbenzothiazole and 4.43% of bitumen, the melt was dissolved in 222...
Embodiment 4
[0049] 20 g of aniline, 80 g of aniline filtrate from the crystallization step and of the same composition as in Example 1 (78% of aniline, 9.5% of 2-mercaptobenzothiazole) were mixed with 28 g of sulfur, 71 g of carbon disulfide and 9 g of The benzothiazole (volatile part) from the washing step was added to the reactor together. Heat the reactor to the working temperature. After the reaction, cool the reactor to 180°C to 200°C, release the accumulated hydrogen sulfide through the pressure control valve, and discharge the material in the reactor at 200°C. Volatile components in the melt were removed by distillation under a reduced pressure of 20 Torr and a temperature of 200°C.
[0050] 161 g of purged melt were obtained, containing 92.2% 2-mercaptobenzothiazole, 1.8% benzothiazole, 1.3% sulfur, 0.7% anilinobenzothiazole, 0.1% symmetric diphenylsulfide Urea, 0.05% of 2-methylbenzothiazole and 3.85% of unidentified substances. This melt was dissolved in a mixture of 222 g of ...
PUM
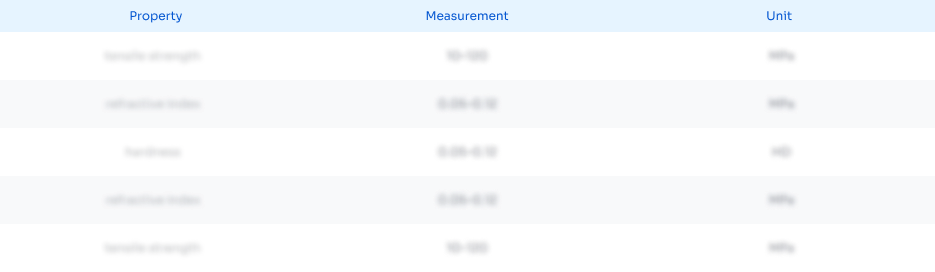
Abstract
Description
Claims
Application Information

- R&D
- Intellectual Property
- Life Sciences
- Materials
- Tech Scout
- Unparalleled Data Quality
- Higher Quality Content
- 60% Fewer Hallucinations
Browse by: Latest US Patents, China's latest patents, Technical Efficacy Thesaurus, Application Domain, Technology Topic, Popular Technical Reports.
© 2025 PatSnap. All rights reserved.Legal|Privacy policy|Modern Slavery Act Transparency Statement|Sitemap|About US| Contact US: help@patsnap.com