Method for forming hollow plastic products and device therefor
A technology of plastic products and molding methods, which is applied in the field of controllable overflow cavity, can solve the problems of product strength reduction, waste of gas energy, product surface air marks, etc., and achieve the goal of improving product qualification rate, prolonging equipment life, and prolonging mold life Effect
- Summary
- Abstract
- Description
- Claims
- Application Information
AI Technical Summary
Problems solved by technology
Method used
Image
Examples
Embodiment Construction
[0019] Below in conjunction with accompanying drawing, feature of the present invention and other relevant features are described in further detail:
[0020] In this embodiment, a plate product with a product thickness of 2-6 mm is used for illustration.
[0021] see figure 1 The middle mark 5 represents the molten plastic in the barrel of the injection molding machine, which is any kind of thermoplastic material that can be used for injection molding; the mark 1 represents the storage barrel of the injection molding machine; 2 represents the injection barrel of the injection molding machine; the mark 4 represents The inner screw of the injection barrel; the mark 3 represents the nozzle; the injection molding machine can be any type of injection molding machine, such as screw type or rod plug type; the mark 6 represents a mold cavity; the cavity 6 can be any traditional injection molding The cavity of the mold; the number 7 indicates the mold; the numbers 9 and 10 respectivel...
PUM
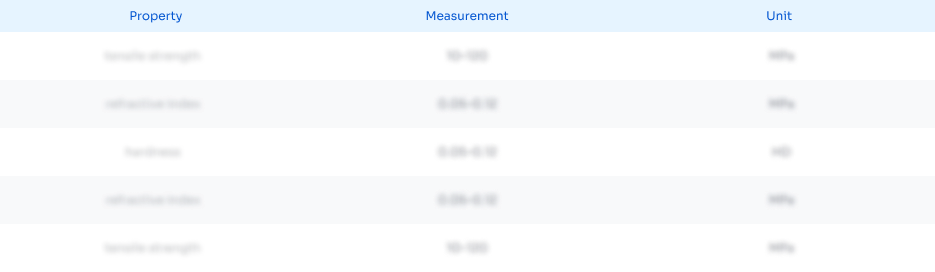
Abstract
Description
Claims
Application Information

- R&D
- Intellectual Property
- Life Sciences
- Materials
- Tech Scout
- Unparalleled Data Quality
- Higher Quality Content
- 60% Fewer Hallucinations
Browse by: Latest US Patents, China's latest patents, Technical Efficacy Thesaurus, Application Domain, Technology Topic, Popular Technical Reports.
© 2025 PatSnap. All rights reserved.Legal|Privacy policy|Modern Slavery Act Transparency Statement|Sitemap|About US| Contact US: help@patsnap.com