Method for producing low-sulfur diesel-oil by oxidation desulfurization
A technology for oxidative desulfurization and oxidizing agent, applied in the direction of refining with oxygenated compounds, can solve problems such as increased cost and high cost, and achieve the effects of reducing production cost, shortening production process, and improving oxidation depth
- Summary
- Abstract
- Description
- Claims
- Application Information
AI Technical Summary
Problems solved by technology
Method used
Image
Examples
Embodiment 1~3
[0035] Get 400 grams of diesel oil (embodiment 1: blended diesel oil, urging firewood: straight firewood=1: 1.5, sulfur-containing 1600 μ g / g; Embodiment 2: Middle East hydrogenated diesel oil, sulfur-containing 650 μ g / g; Embodiment 3: catalyzed diesel oil, Sulfur containing 3000 μg / g) was charged into a stirred reactor, heated to a constant temperature of 90°C while stirring, and mixed industrial hydrogen peroxide (30wt%) and industrial formic acid (85wt%) were continuously added. The total amount of hydrogen peroxide added is 3 times of the chemical demand when all sulfur is converted into sulfone, and the amount of formic acid added is 20 times (mol ratio) of the amount of hydrogen peroxide added. After reacting for 10 minutes, the temperature was lowered, the water phase and the oil phase were separated, and the sulfur content in the oil phase was measured. The analysis data are shown in Table 1.
Embodiment 4~6
[0037] The oil phase separated and obtained in Examples 1-3 is dehydrated and used as the raw material oil for the second-stage oxidation reaction for secondary reaction, and the other conditions are the same as in Examples 1-3. After the reaction, the oil-water phase was separated, and the sulfur content of the oil phase was measured. The results are listed in Table 1.
Embodiment 7~9
[0039] The oil phase separated and obtained in Examples 4-6 is dehydrated and used as the raw material oil for the third-stage oxidation reaction for the third reaction, and the other conditions are the same as those in Examples 1-3. After the reaction, the oil-water phase was separated, and the sulfur content of the oil phase was measured. The results are also listed in Table 1. The results of oxidation desulfurization experiments show that the sulfur content of diesel oil has been significantly reduced after multiple oxidations and separations.
PUM
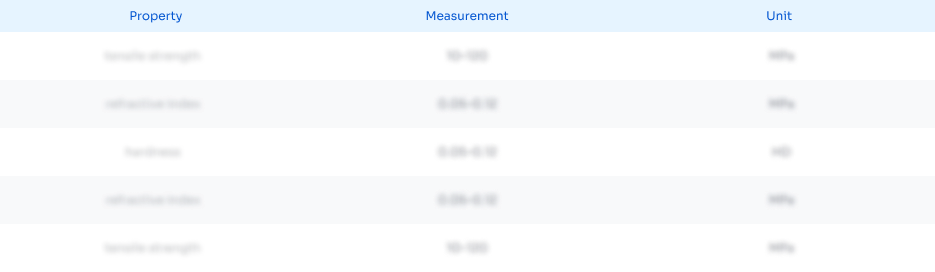
Abstract
Description
Claims
Application Information

- Generate Ideas
- Intellectual Property
- Life Sciences
- Materials
- Tech Scout
- Unparalleled Data Quality
- Higher Quality Content
- 60% Fewer Hallucinations
Browse by: Latest US Patents, China's latest patents, Technical Efficacy Thesaurus, Application Domain, Technology Topic, Popular Technical Reports.
© 2025 PatSnap. All rights reserved.Legal|Privacy policy|Modern Slavery Act Transparency Statement|Sitemap|About US| Contact US: help@patsnap.com