Deformed Al-Mn series alloy and preparing process thereof
A technology for deforming aluminum and manganese systems is applied in the field of aluminum alloy manufacturing to achieve the effects of increased strength, low production cost, and fine and uniform grains
- Summary
- Abstract
- Description
- Claims
- Application Information
AI Technical Summary
Benefits of technology
Problems solved by technology
Method used
Examples
Embodiment 1
[0040] The fine-grained aluminum ingot with a mass fraction of Ti of 0.10% was selected as a raw material to prepare wrought aluminum-manganese alloys, and the mass fraction of Ti in the target product was 0.05%.
[0041] According to the ratio of 0.2% mass fraction of Si in the target product, pure silicon is placed in a melting furnace, preheated to 500°C, and then the fine-grained aluminum ingot melt directly out of the electrolytic cell is added, and pure aluminum of the required quality is added (such as Al 99.70A), so that the mass fraction of molten Ti is 0.05%;
[0042] Using the second injection of refining agent, the temperature of the aluminum melt is reduced to 760 ° C, the first injection is 15 minutes, the injection gas is nitrogen, and the refining agent used is the refining agent for deformed aluminum alloy purchased from the solvent factory;
[0043] Add an aluminum-iron master alloy so that the mass fraction of Fe is 0.50%;
[0044] Add an aluminum-copper ma...
Embodiment 2
[0052] A fine-grained aluminum ingot with a mass fraction of Ti of 0.05% is selected as a raw material to prepare the aluminum alloy of the present invention, and the mass fraction of Ti in the target product is 0.03%.
[0053] The fine-grained aluminum ingot melt directly out of the electrolytic cell is poured into the smelting furnace, and pure aluminum (such as Al 99.70A) of required quality is added so that the mass fraction of Ti in the melt is 0.03%;
[0054] Add manganese additives so that the mass fraction of Mn is 1.2%;
[0055] Add an aluminum-iron master alloy so that the mass fraction of Fe is 0.45%;
[0056] Add an aluminum-copper master alloy so that the mass fraction of Cu is 0.05%;
[0057] Add aluminum-silicon master alloy so that the mass fraction of Si is 0.45%,
[0058] Add aluminum rare earth master alloy (cerium-rich mixed rare earth), so that the mass fraction of rare earth is 0.30%;
[0059]Analyze the melt composition, if the mass fraction of Ti is ...
Embodiment 3
[0065] A fine-grained aluminum ingot with a mass fraction of Ti of 0.03% is selected as a raw material to prepare the aluminum alloy of the present invention, and the mass fraction of Ti in the target product is 0.015%.
[0066] The fine-grained aluminum ingot melt directly out of the electrolytic cell is poured into the smelting furnace, and the required mass of pure aluminum is added so that the mass fraction of Ti in the melt is 0.015%;
[0067] Add an aluminum-iron master alloy so that the mass fraction of Fe is 0.50%;
[0068] Add manganese additives so that the mass fraction of Mn is 0.95%;
[0069] Add copper additives so that the mass fraction of Cu is 0.05%;
[0070] Add aluminum rare earth master alloy (lanthanum-rich mixed rare earth), so that the mass fraction of rare earth is 0.25%;
[0071] Analyze the composition of the melt. If the mass fraction of Ti is lower than 0.010%, add aluminum and aluminum alloys to supplement it with titanium additives. If it is hig...
PUM
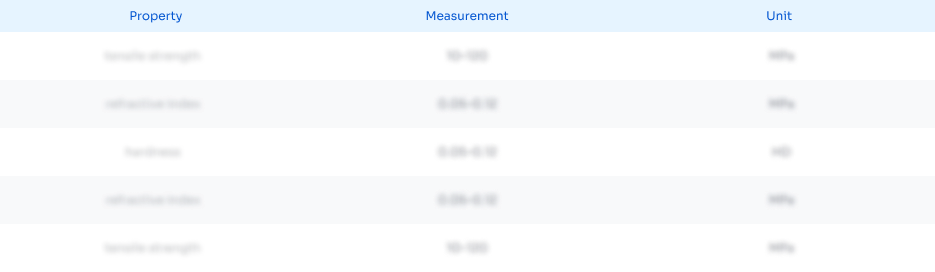
Abstract
Description
Claims
Application Information

- Generate Ideas
- Intellectual Property
- Life Sciences
- Materials
- Tech Scout
- Unparalleled Data Quality
- Higher Quality Content
- 60% Fewer Hallucinations
Browse by: Latest US Patents, China's latest patents, Technical Efficacy Thesaurus, Application Domain, Technology Topic, Popular Technical Reports.
© 2025 PatSnap. All rights reserved.Legal|Privacy policy|Modern Slavery Act Transparency Statement|Sitemap|About US| Contact US: help@patsnap.com