Adjustable casting mold
A mold and cold casting technology used in the field of molds for direct cold casting of metal ingots
- Summary
- Abstract
- Description
- Claims
- Application Information
AI Technical Summary
Problems solved by technology
Method used
Image
Examples
Embodiment Construction
[0038] Figure 1 shows the main components of a preferred adjustable mold assembly 15 of the present invention. The die assembly 15 includes a pair of opposing side walls 16 and a pair of opposing end walls 17 that together define a generally rectangular die space 100 having an open top through which molten metal enters the die 15 . The relatively longer side walls 16 are substantially parallel to each other and to the longitudinal axis L. As shown in FIG. The relatively short end walls 17 are parallel to each other and to the transverse axis T. As shown in FIG. The broad faces and short edges of the ingot (not shown) are formed along the side walls 16 and along the end walls 17 . The nominal width w of the ingot is defined by the longitudinal distance between the end walls 17 , while the nominal thickness t of the ingot is defined by the length of the end walls 17 (measured parallel to the transverse axis T).
[0039] Each side wall 16 has a first end 102, a second end 104, ...
PUM
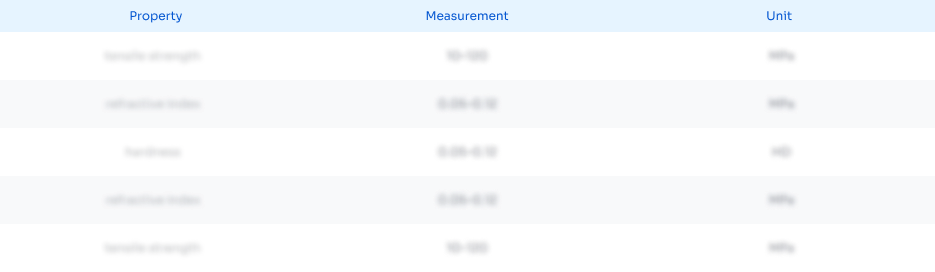
Abstract
Description
Claims
Application Information

- R&D Engineer
- R&D Manager
- IP Professional
- Industry Leading Data Capabilities
- Powerful AI technology
- Patent DNA Extraction
Browse by: Latest US Patents, China's latest patents, Technical Efficacy Thesaurus, Application Domain, Technology Topic, Popular Technical Reports.
© 2024 PatSnap. All rights reserved.Legal|Privacy policy|Modern Slavery Act Transparency Statement|Sitemap|About US| Contact US: help@patsnap.com