Matrix form push installing method for large span deep space steel structure
A steel structure, large-span technology, applied in building structure, construction, etc., can solve problems such as inability to install tire frames and cranes, low rigidity, etc.
- Summary
- Abstract
- Description
- Claims
- Application Information
AI Technical Summary
Problems solved by technology
Method used
Image
Examples
Embodiment Construction
[0010] In Figures 1, 2, 3, 4, and 5, a flat tire frame 1 and a vertical tire frame 2 are arranged on a span end of the space steel structure installation position, and a slideway 3 is arranged on the vertical column position of the space steel structure. Assemble the first main truss 4 on the flat tire frame 1, hoist the first main truss 4 to the vertical tire frame 2 with the crane 5 to assemble the first main truss 4 and the column 6, and install anti-friction blocks at the bottom of the column 6 7. Simultaneously install a pushing device (hydraulic jack 10) and a counterforce frame 8 at the bottom of the column 6, and the counterforce frame 8 is inserted into the support position 9, thereby forming a steel structure jacking matrix. The structure of integrating the first main truss 4 and the column 6 is pushed and translated by the pusher along the slideway 3 by a column distance, and then the second tire frame 1 and the vertical tire frame 2 are assembled at the end of the s...
PUM
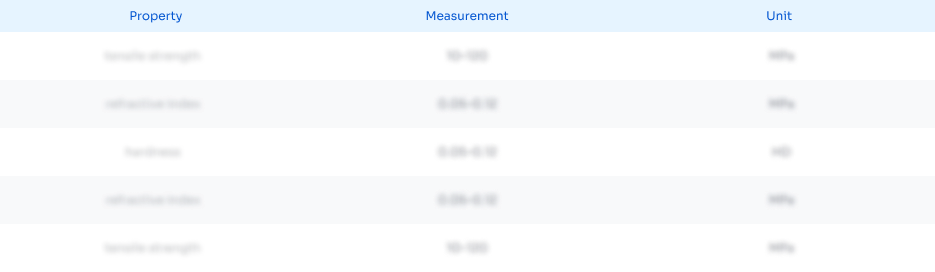
Abstract
Description
Claims
Application Information

- Generate Ideas
- Intellectual Property
- Life Sciences
- Materials
- Tech Scout
- Unparalleled Data Quality
- Higher Quality Content
- 60% Fewer Hallucinations
Browse by: Latest US Patents, China's latest patents, Technical Efficacy Thesaurus, Application Domain, Technology Topic, Popular Technical Reports.
© 2025 PatSnap. All rights reserved.Legal|Privacy policy|Modern Slavery Act Transparency Statement|Sitemap|About US| Contact US: help@patsnap.com