Anti-knock container
A container and outer cylinder technology, applied in the field of anti-explosion containers, can solve the problems of difficult gas discharge, small capacity of anti-explosion containers, thread wear, etc., to reduce shock wave overpressure and noise, improve anti-explosion and explosion-proof performance, anti-explosion Good explosion-proof performance
- Summary
- Abstract
- Description
- Claims
- Application Information
AI Technical Summary
Problems solved by technology
Method used
Image
Examples
Embodiment Construction
[0015] The present invention will be further described below with reference to the accompanying drawings and examples.
[0016] Such as figure 1 , figure 2 and image 3 As shown, the anti-explosion container has an upper cover 1, a cylinder body 10 and a fixed bracket 9 welded on the bottom of the cylinder body. The cylinder body 10 is composed of an outer cylinder 5 and an inner cylinder 6. The upper end of the outer cylinder 6 is open, and the lower end has a An integrated bottom head 13, the lower part of the inner cylinder 5 has a lower wave breaking plate 8, and the upper cover 1 is composed of a top cover plate 17 and a cylindrical cover wall 20, wherein the lower end of the cover wall 20 is provided with an upper wave breaking plate 3, and the cover wall 20 Splines 19 are arranged on the top, which can be connected with the spline collar 11 on the inner side of the upper port of the outer tube 6 , and the top cover plate 17 is equipped with explosion-venting bolts 15...
PUM
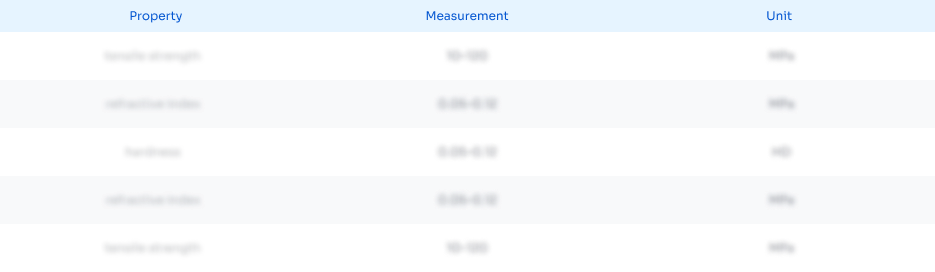
Abstract
Description
Claims
Application Information

- R&D
- Intellectual Property
- Life Sciences
- Materials
- Tech Scout
- Unparalleled Data Quality
- Higher Quality Content
- 60% Fewer Hallucinations
Browse by: Latest US Patents, China's latest patents, Technical Efficacy Thesaurus, Application Domain, Technology Topic, Popular Technical Reports.
© 2025 PatSnap. All rights reserved.Legal|Privacy policy|Modern Slavery Act Transparency Statement|Sitemap|About US| Contact US: help@patsnap.com