Three-dimensional ultrasonic imaging non-destructive inspection system
A three-dimensional ultrasonic and non-destructive flaw detection technology, which is used in material analysis, image data processing, and 3D image processing using sonic/ultrasonic/infrasonic waves. It can achieve the objective of detection results, avoid subjectivity, and achieve the effect of practical and comprehensive detection.
- Summary
- Abstract
- Description
- Claims
- Application Information
AI Technical Summary
Problems solved by technology
Method used
Image
Examples
Embodiment Construction
[0014] Below in conjunction with accompanying drawing, the present invention is described in further detail:
[0015] The present invention is made up of three major parts.
[0016] The first part is a computer platform (11), i.e. a general-purpose computer platform, including a bus (6) providing channels for various information transmissions. The computing power of the CPU used by the general-purpose microcomputer should be as large as possible (each channel needs Pentium III 1GMHz or equivalent computing power) to meet the requirements of increasing the number of channels; the motherboard used should use standard 32-bit or 64-bit PCI Bus, the frequency of PCI can be selected not less than 33MHz (such as 33MHz, 66MHz or 100MHz or even higher) to meet the requirements of multi-channel high data transmission rate, and the number of PCI slots on it should not be less than 4 to adapt to multi-channel The motherboard should support disk array RAID; the memory should be no less th...
PUM
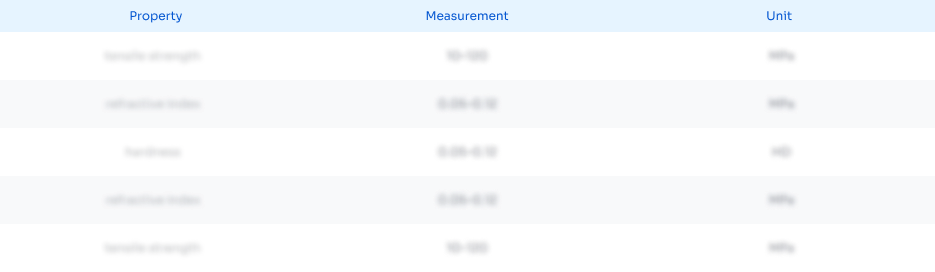
Abstract
Description
Claims
Application Information

- Generate Ideas
- Intellectual Property
- Life Sciences
- Materials
- Tech Scout
- Unparalleled Data Quality
- Higher Quality Content
- 60% Fewer Hallucinations
Browse by: Latest US Patents, China's latest patents, Technical Efficacy Thesaurus, Application Domain, Technology Topic, Popular Technical Reports.
© 2025 PatSnap. All rights reserved.Legal|Privacy policy|Modern Slavery Act Transparency Statement|Sitemap|About US| Contact US: help@patsnap.com