Cartalyst for preparing hydrogen without COx by ammonia decompsition reaction and preparing method thereof
A catalyst and ammonia decomposition technology, applied in the direction of catalyst activation/preparation, catalyst carrier, chemical instruments and methods, etc., can solve the problems of difficult to meet high-efficiency production of hydrogen, low catalyst activity, etc., achieve low cost, simple preparation process, high active effect
- Summary
- Abstract
- Description
- Claims
- Application Information
AI Technical Summary
Benefits of technology
Problems solved by technology
Method used
Image
Examples
Embodiment 1
[0021] Take 0.1081g RuCl 3 Dissolve in 10ml of acetone to form a solution, then mix with 1g of carbon nanotubes, stir for 1h, then dry at 55°C for 5h, then raise the temperature to 500°C at 10°C / min, and bake at this temperature for 10h. Get 0.05g catalyst (the content of Ru is 5%) and put in quartz reactor, under 25%H 2 -In the Ar atmosphere (80ml / min), the temperature was raised to 550°C at 5°C / min, and activated at this temperature for 2h, and then high-purity ammonia gas was introduced to react at 550°C, and the flow rate of ammonia gas was 50ml / min. Reaction results: the conversion rate of ammonia is 91.2%, and the generation rate of hydrogen is 61.1mmol / (min·g-cat); the stability of the catalyst is shown in the attached figure 1 .
Embodiment 2
[0023] Take 0.0313g RuCl 3 Dissolve in 10ml of acetone to form a solution, then mix with 1g of carbon nanotubes, stir for 1 hour, then dry at 85°C for 12 hours, then raise the temperature to 600°C at 2°C / min, and bake at this temperature for 2 hours. Get 0.05g catalyst (the content of Ru is 1.5%) and put in the quartz reactor, under 25% H 2 -In the Ar atmosphere (50ml / min), the temperature was raised to 400°C at 10°C / min, and activated at this temperature for 32h, and then high-purity ammonia gas was introduced to react at 550°C, and the flow rate of ammonia gas was 50ml / min. Reaction results: the conversion rate of ammonia was 75.5%, and the generation rate of hydrogen was 50.5 mmol / (min·g-cat).
Embodiment 3
[0025] Take 0.0309g RuCl 3 Dissolve in 30ml of acetone to form a solution, mix these solutions with 3g of carbon nanotubes, stir for 1 hour, then dry at 100°C for 8 hours, then raise the temperature to 400°C at 2°C / min, roast at this temperature for 5 hours and cool, then pass into 25%H 2 -Ar (150ml / min) was calcined at 500°C for 2h. Take 0.51g La(NO 3 ) 3 Dissolved in 30ml of water to form a solution, mixed with these calcined catalysts, dried at 55°C for 10h, and then calcined at 400°C for 2h to obtain a catalyst. Get 0.1g catalyst (Ru content is 0.46%, La content is 6.74%) and is put in quartz reactor, under 25% H 2 -In an Ar atmosphere (80ml / min), the temperature was raised to 500°C at 10°C / min, and activated at this temperature for 50h, and then high-purity ammonia gas was introduced to react at 550°C, and the flow rate of ammonia gas was 100ml / min. Reaction result: the conversion rate of ammonia is 63.8%, and the generation rate of hydrogen is 42.7mmol / (min·g-cat). ...
PUM
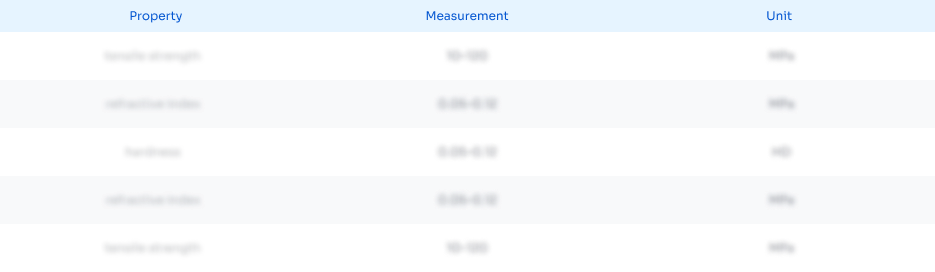
Abstract
Description
Claims
Application Information

- R&D Engineer
- R&D Manager
- IP Professional
- Industry Leading Data Capabilities
- Powerful AI technology
- Patent DNA Extraction
Browse by: Latest US Patents, China's latest patents, Technical Efficacy Thesaurus, Application Domain, Technology Topic, Popular Technical Reports.
© 2024 PatSnap. All rights reserved.Legal|Privacy policy|Modern Slavery Act Transparency Statement|Sitemap|About US| Contact US: help@patsnap.com