Robot arm mechanism and robot device
A technology of robotic arms and connectors, used in transportation and packaging, claw arms, manipulators, etc.
- Summary
- Abstract
- Description
- Claims
- Application Information
AI Technical Summary
Problems solved by technology
Method used
Image
Examples
Embodiment Construction
[0038] now refer to Figure 1-15 Embodiments of a robot arm mechanism and a robot device according to the present invention are described. Throughout the following detailed description, like reference symbols and numerals refer respectively to like parts throughout the drawings.
[0039] A first embodiment of a robot arm mechanism and a robot device according to the invention will be referred to in the appended Figure 1-5 be described first.
[0040] figure 1 and 2 The illustrated robotic arm mechanism 110 includes a first handling member 116 for supporting and handling a first object, and a second handling member 117 for supporting and handling a second object. The configuration of the first and second handling members 116 and 117 can be used for handling, ie, holding and releasing a wafer and other materials for producing semiconductors. The structures of the first and second manipulating parts 116 and 117 depend on the size and shape of the material processed by the f...
PUM
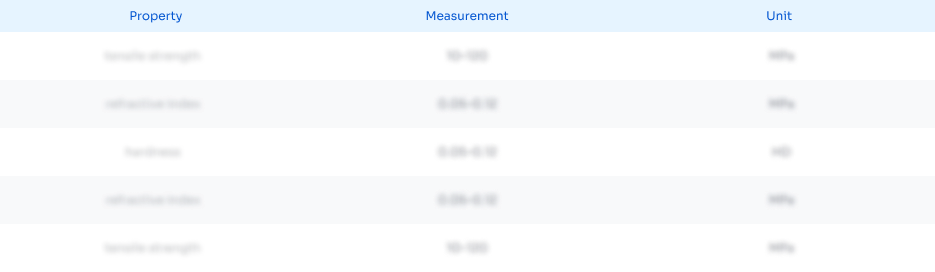
Abstract
Description
Claims
Application Information

- R&D
- Intellectual Property
- Life Sciences
- Materials
- Tech Scout
- Unparalleled Data Quality
- Higher Quality Content
- 60% Fewer Hallucinations
Browse by: Latest US Patents, China's latest patents, Technical Efficacy Thesaurus, Application Domain, Technology Topic, Popular Technical Reports.
© 2025 PatSnap. All rights reserved.Legal|Privacy policy|Modern Slavery Act Transparency Statement|Sitemap|About US| Contact US: help@patsnap.com