Rotary kiln with resistor furnace for heating and calcining kaolin
A technology of calcining kaolin and rotary kiln, which is applied to lighting and heating equipment, furnaces, drum furnaces, etc., to achieve the effects of stable product quality, simplified thermal control, and low equipment manufacturing prices
- Summary
- Abstract
- Description
- Claims
- Application Information
AI Technical Summary
Problems solved by technology
Method used
Image
Examples
Embodiment Construction
[0015] Figure 1 and figure 2 The kaolin calcined kaolin rotary kiln shown in resistance furnace includes calcined rotary kiln body 1, supporting wheel 2, feed end 3, discharge end 4, feeding mechanism 5 and motor 6, reduction box 7, pinion 8 and large The transmission mechanism composed of gear 9 and the resistance furnace 19; the supporting wheel 2 supports the calcining rotary kiln body 1 through the supporting belt 10 fixed at both ends of the calcining rotary kiln body 1; the large gear 9 in the transmission mechanism is installed in the calcining rotary kiln kiln One end of the kiln body 1, the motor 6 drives the pinion 8 to rotate through the reduction box 7, and the pinion 8 rotates the calcining rotary kiln body 1 through the large gear 9; The two ends of the kiln are connected flexibly, the feeding mechanism 5 is connected with the feeding end 3, and the resistance furnace 19 is arranged at the bottom of the calcining rotary kiln body 1.
[0016] In order to make the...
PUM
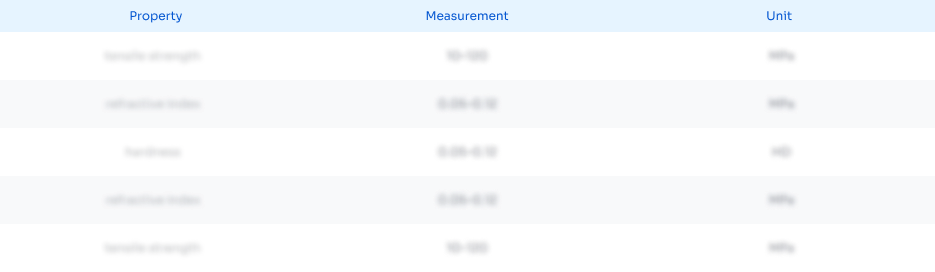
Abstract
Description
Claims
Application Information

- R&D Engineer
- R&D Manager
- IP Professional
- Industry Leading Data Capabilities
- Powerful AI technology
- Patent DNA Extraction
Browse by: Latest US Patents, China's latest patents, Technical Efficacy Thesaurus, Application Domain, Technology Topic, Popular Technical Reports.
© 2024 PatSnap. All rights reserved.Legal|Privacy policy|Modern Slavery Act Transparency Statement|Sitemap|About US| Contact US: help@patsnap.com