Improved coextruder for forming multi-layer composite plastic pipe
A technology of co-extrusion molding and multi-layer compounding, which is applied in the field of multi-layer composite plastic pipe co-extrusion molding devices, can solve the problems of narrow processing range, influence on extruder efficiency, material mixing and homogenization effect, and poor flow uniformity. Achieve the effect of no stagnant material dead angle, good production flexibility and versatility, and good material mixing and homogenization effect
- Summary
- Abstract
- Description
- Claims
- Application Information
AI Technical Summary
Problems solved by technology
Method used
Image
Examples
Embodiment
[0015] Embodiment: Referring to the accompanying drawings, the three-layer composite plastic pipe co-extrusion molding device is composed of a combined co-extrusion feeding body 1, a basic die body 2, an adapter connector 3, and a die assembly 4. Four modules are combined, In order to ensure the concentricity and connection accuracy of each component combination, the connection of adjacent parts (parts) adopts concave-convex steps 5 and / or positioning pins / holes 6. In order to facilitate disassembly and assembly, each part (part) has a through ejector Bolt 7. The combined co-extrusion feed body 1 is composed of a feed block 1.1 and a feed block 1.2, wherein the feed block 1.1 has an outer layer feed port 1.3 and a middle layer feed port 1.4, and the feed block 1.2 has a The inner layer feed port is 1.5, and each feed port is connected to three extruders respectively. The axes of the three extruders are arranged at 45° adjacent to each other. There are through air intake holes...
PUM
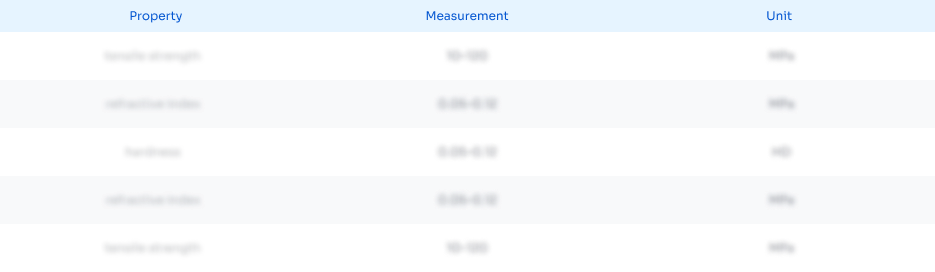
Abstract
Description
Claims
Application Information

- Generate Ideas
- Intellectual Property
- Life Sciences
- Materials
- Tech Scout
- Unparalleled Data Quality
- Higher Quality Content
- 60% Fewer Hallucinations
Browse by: Latest US Patents, China's latest patents, Technical Efficacy Thesaurus, Application Domain, Technology Topic, Popular Technical Reports.
© 2025 PatSnap. All rights reserved.Legal|Privacy policy|Modern Slavery Act Transparency Statement|Sitemap|About US| Contact US: help@patsnap.com