Process for preparing high water absorption resin
A super absorbent resin, water-soluble technology, applied in the field of chemical engineering, can solve the problems of complex product crushing and post-processing, difficult heat transfer and stirring, low water absorption, etc. The effect of speed increase
- Summary
- Abstract
- Description
- Claims
- Application Information
AI Technical Summary
Problems solved by technology
Method used
Image
Examples
Embodiment 1
[0028] Weigh 5.785g of sodium hydroxide, dissolve in 40ml of deionized water, and cool to room temperature. Measure 13.5 milliliters of acrylic acid (rectified under reduced pressure) in the beaker, under stirring, sodium hydroxide aqueous solution is slowly introduced into acrylic acid for neutralization reaction, after cooling, add 2.415 g of the second monomer methacrylamide and 0.006 g of 1,3- Propylene Glycol Crosslinker, stir until completely dissolved.
[0029] Add 0.8g of Span 80, 0.4g of Tween 20 and 130ml of n-hexane into a 500ml 4-port jacketed reactor with a thermometer, stir and dissolve at room temperature, then add the above monomer aqueous solution and initiator isopropyl peroxide Add 0.09g of benzene, and add 0.006g of polyethylene glycol dimethacrylate into the reaction kettle at the same time, pass nitrogen and exhaust oxygen, heat up to 50°C after cold stirring, and react for 2 hours. After the reaction was completed, water was removed azeotropically at 80...
Embodiment 2
[0032] Weigh 4.235g of sodium hydroxide, dissolve in 30ml of deionized water, and cool to room temperature. Measure 12.1 milliliters of acrylic acid (rectified under reduced pressure) in the beaker, under stirring, sodium hydroxide aqueous solution is slowly introduced into acrylic acid for neutralization reaction, after cooling, add 1.625 g of the second monomer methyl acrylate and 0.004 g of 1-ethyl- 3-[3-(Dimethylamino)propyl]carbodiimide, stirred until completely dissolved.
[0033] Add 0.8g dispersant Span 65 and 170 milliliters of hexanaphthene into 500 milliliters of jacketed reaction kettles with 4 outlets of thermometer, stir and dissolve at room temperature, then add above-mentioned aqueous monomer solution and initiator potassium persulfate 0.05g, and Add 0.004g of ethylene glycol dimethacrylate, pass nitrogen and exhaust oxygen, heat up to 65°C after cold stirring, and react for 0.5 hours. After the reaction was completed, water was removed azeotropically at 90°C....
Embodiment 3
[0036] Weigh 7.398g of potassium hydroxide, dissolve in 30ml of deionized water, and cool to room temperature. Measure 12.5 milliliters of acrylic acid (rectified under reduced pressure), slowly introduce potassium hydroxide aqueous solution into acrylic acid for neutralization reaction under stirring, add 0.075 g of the second monomer methacrylic acid and 0.004 g of glutaraldehyde after cooling, and stir until completely dissolve.
[0037] Add 0.8 g of dispersant Span 60 and 170 ml of toluene into a 500 ml 4-hole jacketed reactor with a thermometer, stir and dissolve at room temperature, then add the above-mentioned monomer aqueous solution and 0.05 g of initiator ammonium persulfate, and discharge through nitrogen. Oxygen, after cold stirring, the temperature was raised to 65°C, and reacted for 1 hour, and 0.054 g of ethylene glycol diacrylate was added into the reaction kettle, and the reaction was continued for 1 hour. After the reaction was completed, water was removed a...
PUM
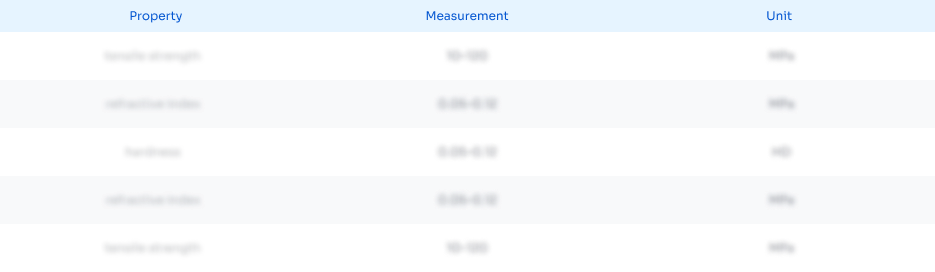
Abstract
Description
Claims
Application Information

- R&D
- Intellectual Property
- Life Sciences
- Materials
- Tech Scout
- Unparalleled Data Quality
- Higher Quality Content
- 60% Fewer Hallucinations
Browse by: Latest US Patents, China's latest patents, Technical Efficacy Thesaurus, Application Domain, Technology Topic, Popular Technical Reports.
© 2025 PatSnap. All rights reserved.Legal|Privacy policy|Modern Slavery Act Transparency Statement|Sitemap|About US| Contact US: help@patsnap.com