Six-degree-of-freedom automatic path optimization intelligent welding platform and method
An automatic optimization, welding platform technology, applied in welding equipment, auxiliary welding equipment, welding/cutting auxiliary equipment, etc., can solve the problems of not being able to complete the welding at one time, the accuracy cannot be guaranteed, and the completion can not be completed, so as to break through the limitation of space arm length. , Improve the accuracy and process quality, reduce the effect of the process of handling
- Summary
- Abstract
- Description
- Claims
- Application Information
AI Technical Summary
Problems solved by technology
Method used
Image
Examples
Embodiment 1
[0042] This embodiment proposes a six-degree-of-freedom automatic optimization path intelligent welding platform, such as Figure 1-3 As shown, the intelligent welding platform with six degrees of freedom automatically optimizes the path includes a welding platform system, the welding platform system is connected with a trolley system, a robot is set on the trolley system, and an intelligent control system controls the robot Weld.
[0043] In the intelligent welding platform with six degrees of freedom automatically optimizing the path described in this embodiment, the welding platform system is connected with the trolley system. On the one hand, this setting enhances the support stability of the welding platform system; Support stability; in addition, it also realizes the intelligent positioning function with three degrees of freedom and large motion range, which improves the welding accuracy. The robot is set on the trolley system, which enables the trolley system to provid...
Embodiment 2
[0091] This embodiment proposes a six-degree-of-freedom automatic optimization path intelligent welding method, and the six-degree-of-freedom automatic optimization path intelligent welding method uses the six-degree-of-freedom automatic optimization path intelligent welding platform described in Embodiment 1, like Figure 4 As shown, the large-scale intelligent welding method for automatically optimizing a path with six degrees of freedom includes the following steps:
[0092] S1, start;
[0093] Step S1 specifically includes the following steps:
[0094] S11. Start:
[0095] S12, the device returns to zero and the system is reset.
[0096] Specifically, step S12 is for the operator to control the reset of the device zero return system.
[0097] S2, clamping the workpiece;
[0098] Step S2 specifically includes the following steps:
[0099] S21, clamping the workpiece.
[0100] Specifically, the operator clamps the workpiece on the welding work platform 7 .
[0101] M...
PUM
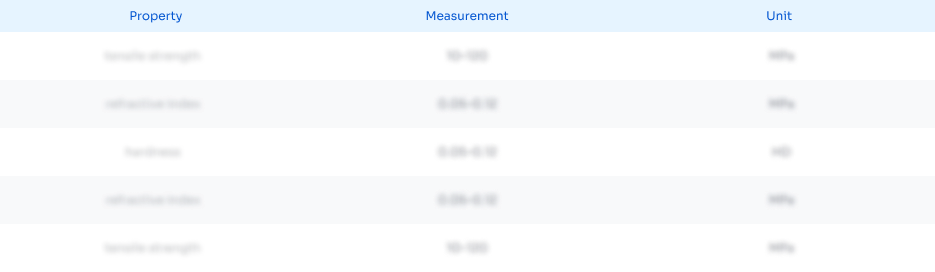
Abstract
Description
Claims
Application Information

- Generate Ideas
- Intellectual Property
- Life Sciences
- Materials
- Tech Scout
- Unparalleled Data Quality
- Higher Quality Content
- 60% Fewer Hallucinations
Browse by: Latest US Patents, China's latest patents, Technical Efficacy Thesaurus, Application Domain, Technology Topic, Popular Technical Reports.
© 2025 PatSnap. All rights reserved.Legal|Privacy policy|Modern Slavery Act Transparency Statement|Sitemap|About US| Contact US: help@patsnap.com