Control method and system for assisting servo motor driving through weighing and displacement sensor
A displacement sensor, load cell technology, applied in electrical program control, program control in sequence/logic controllers, etc., can solve the problems of inaccurate pressing force and displacement accuracy, and achieve the problem of inaccurate pressing force and displacement accuracy. Accurate, guaranteed repeat accuracy, safe and reliable equipment
- Summary
- Abstract
- Description
- Claims
- Application Information
AI Technical Summary
Problems solved by technology
Method used
Image
Examples
Embodiment approach 1
[0041] Embodiment 1. A control method for assisting the drive of a servo motor by a weighing and displacement sensor described in this embodiment, refer to figure 1 This embodiment can be better understood, including the following steps:
[0042] Step S1, the control device determines the coding value according to the process design position of the pressing equipment, and the encoder of each position determines the coding value according to the feedback value of the micro-pulse displacement sensor;
[0043] Step S2, the frequency converter drives the servo motor according to the determined code value, the control device monitors the real-time position of the pressing equipment in real time through the micro-pulse displacement sensor, and starts the protection function when the real-time position exceeds a reasonable range;
[0044] Step S3, the control device monitors the pressure value of the pressing equipment in real time through the weighing sensor, and starts the protecti...
Embodiment approach 2
[0047] Embodiment 2. This embodiment is a further limitation of the control method described in Embodiment 1, which is driven by a weighing and displacement sensor assisted by a servo motor. In this embodiment, in step S1, the control The device is a PLC programmable controller.
Embodiment approach 3
[0048] Embodiment 3. This embodiment is a further limitation of the control method described in Embodiment 1, which is driven by a weighing and displacement sensor assisted by a servo motor. In this embodiment, in step S2, the reasonable The range is that the accuracy is greater than 0mm and less than or equal to 0.1mm.
[0049] In this embodiment, the micro-pulse displacement sensor is used for auxiliary control to ensure the accuracy and repeatability of the servo-driven pressing device in place.
PUM
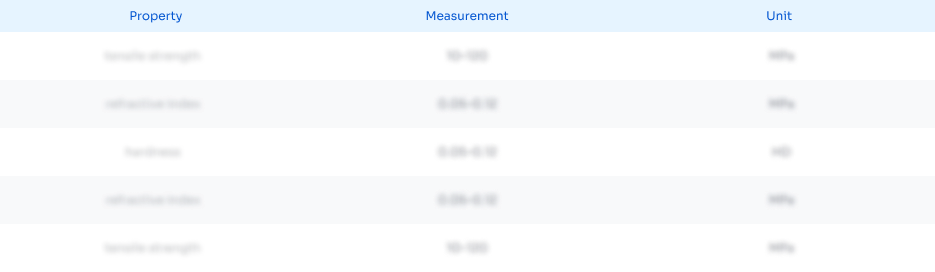
Abstract
Description
Claims
Application Information

- R&D Engineer
- R&D Manager
- IP Professional
- Industry Leading Data Capabilities
- Powerful AI technology
- Patent DNA Extraction
Browse by: Latest US Patents, China's latest patents, Technical Efficacy Thesaurus, Application Domain, Technology Topic, Popular Technical Reports.
© 2024 PatSnap. All rights reserved.Legal|Privacy policy|Modern Slavery Act Transparency Statement|Sitemap|About US| Contact US: help@patsnap.com