Flame-retardant epoxy resin composition
A technology of epoxy resin and brominated epoxy resin, applied in the field of vacuum infusion technology
- Summary
- Abstract
- Description
- Claims
- Application Information
AI Technical Summary
Problems solved by technology
Method used
Image
Examples
Embodiment 1
[0105] Example 1 (Ex1)
[0106] 62.5g of D.E.R.331 and 22g of ICL F2016 were placed in a container, heated to 80°C with stirring, and cooled to room temperature after the brominated epoxy resin was completely dissolved in the epoxy resin. Subsequently, 15 g of organic phosphorus flame retardant TEP and 0.5 g of KH570 were added, and the epoxy resin component was obtained after mixing with a paddle stirrer for about 20 minutes.
Embodiment 2
[0107] Example 2 (Ex2)
[0108] 49.4g of D.E.R.338, 22g of NPEB 400, 10g of diluent ERISYS GE21 and 18.1g of organophosphorus flame retardant DEEP and 0.5g of KH570 were placed in a closed container and stirred at room temperature for 2 hours until a brominated ring was obtained A homogeneous resin mixture in which the oxygen resin is completely dissolved, an epoxy resin component is obtained.
Embodiment 3
[0109] Example 3 (Ex3)
[0110] 40g of D.E.R.331, 22g of NPEB 400, 19.5g of diluent trimethylolpropane triglycidyl ether, 18g of organophosphorus flame retardant DEEP and 0.5g of KH570 were placed in a closed container and stirred at room temperature for 2 hours until a homogeneous resin mixture in which the brominated epoxy resin is completely dissolved is obtained, that is, the epoxy resin component is obtained.
PUM
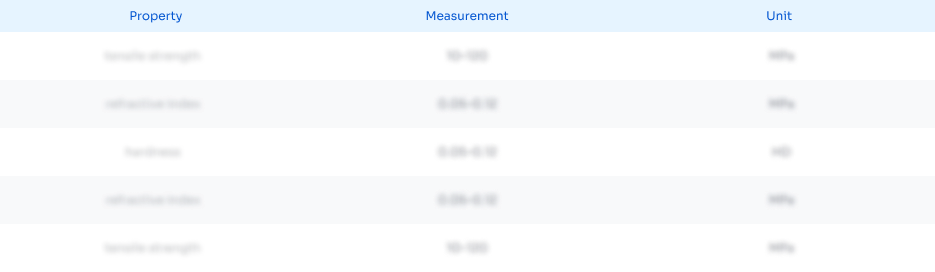
Abstract
Description
Claims
Application Information

- R&D Engineer
- R&D Manager
- IP Professional
- Industry Leading Data Capabilities
- Powerful AI technology
- Patent DNA Extraction
Browse by: Latest US Patents, China's latest patents, Technical Efficacy Thesaurus, Application Domain, Technology Topic, Popular Technical Reports.
© 2024 PatSnap. All rights reserved.Legal|Privacy policy|Modern Slavery Act Transparency Statement|Sitemap|About US| Contact US: help@patsnap.com