Intelligent vibration reduction cooperative system applied to high-speed train and control method of intelligent vibration reduction cooperative system
An intelligent vibration reduction, high-speed train technology, applied in the direction of the device for lateral relative movement between the underframe and the bogie, can solve problems such as reducing the resistance force
- Summary
- Abstract
- Description
- Claims
- Application Information
AI Technical Summary
Problems solved by technology
Method used
Image
Examples
specific Embodiment 1
[0045] Specific embodiment 1, the sensing unit includes a first inclination sensor, a second inclination sensor and a speed sensor provided on the head vehicle, the first inclination sensor is installed on the vehicle body, and is used for measuring the roll angle of the vehicle body; The second inclination sensor is installed on the front bogie frame and is used to measure the roll angle of the frame; the speed sensor is used to detect the running speed of the train, and the vibration damping unit includes a lateral damper and an anti-serpentine damper , the cooperative controller is signal-connected to the lateral shock absorber and the anti-serpentine shock absorber.
[0046] Attached to the manual Figure 8 As shown, the body roll angle and the frame roll angle are both used to measure the inclination angle between the body and the horizontal plane, and three mutually perpendicular coordinate axes x, y, and z are drawn through the center of gravity O of the body. It has 6...
specific Embodiment 2
[0059] An intelligent vibration-damping collaborative control method applied to high-speed trains, the method is based on an intelligent vibration-damping collaborative system applied to high-speed trains, and includes a preprocessing step and an application step, wherein the preprocessing step includes:
[0060] S1-1, linearize the damping data to obtain the range of damping coefficients output by the lateral shock absorber and the anti-serpentine shock absorber, as well as the input current and output damping of the lateral shock absorber and the anti-serpentine shock absorber the corresponding relationship of the coefficients, and adjust the threshold value of the control current output by the cooperative controller to the lateral vibration damper and the anti-serpentine vibration damper, so that the control current output by the cooperative controller and the lateral vibration damping Linear alignment of the damping coefficient output by the damper and the anti-serpentine s...
specific Embodiment 3
[0073] When the speed is greater than 200km / h and less than 220km / h, and both the first inclination sensor and the second inclination sensor are lower than the set value (use q 1 and q 2When the train is running in a straight line, the cooperative controller converts the corresponding damping coefficient into a current regulation value and inputs it to the two types of shock absorbers, and the two types of shock absorbers provide the corresponding damping force;
[0074] When the speed is greater than 200km / h and less than 220km / h, and both the first inclination sensor and the second inclination sensor are greater than the set value, the train is passing through the curve, and the cooperative controller inputs the corresponding current regulation value to the two types of vibration reduction The two types of shock absorbers provide corresponding damping force;
[0075] In the state judgment step, when the speed range is between 200km / h-220km / h, record the collection value of ...
PUM
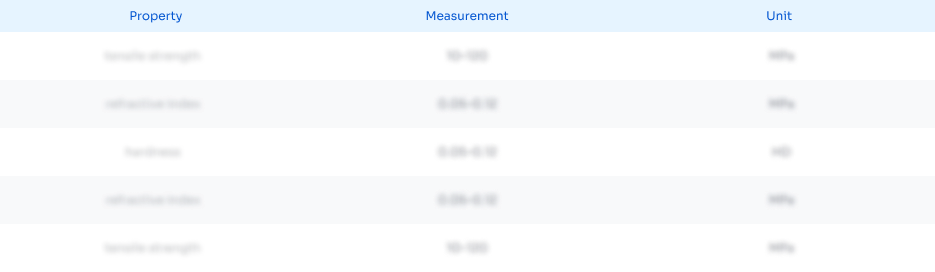
Abstract
Description
Claims
Application Information

- Generate Ideas
- Intellectual Property
- Life Sciences
- Materials
- Tech Scout
- Unparalleled Data Quality
- Higher Quality Content
- 60% Fewer Hallucinations
Browse by: Latest US Patents, China's latest patents, Technical Efficacy Thesaurus, Application Domain, Technology Topic, Popular Technical Reports.
© 2025 PatSnap. All rights reserved.Legal|Privacy policy|Modern Slavery Act Transparency Statement|Sitemap|About US| Contact US: help@patsnap.com