Robot path generation method for hub hole deburring machining
A path generation and processing path technology, applied in the direction of manipulators, manufacturing tools, program control manipulators, etc., can solve the problems of large number of path points, unfavorable modification, poor processing effect, etc., achieve smooth attitude transition, reduce collisions, and pose Optimized effect
- Summary
- Abstract
- Description
- Claims
- Application Information
AI Technical Summary
Problems solved by technology
Method used
Image
Examples
Embodiment Construction
[0021] The specific implementation of the present invention will be described in further detail below by describing the embodiments with reference to the accompanying drawings, so as to help those skilled in the art have a more complete, accurate and in-depth understanding of the inventive concepts and technical solutions of the present invention.
[0022] figure 1 It is a flowchart of a robot path generation method for wheel hub hole deburring provided by an embodiment of the present invention. The method specifically includes the following steps:
[0023] S1. Import the hub image into the OpenCASCADE software, select the hub hole to be deburred, generate the deburring processing path corresponding to the side of the wheel hole, put it into the path set {P}, and generate a deburring process for each side of the wheel hole The deburring processing path and the deburring processing path are composed of discrete path point sequences;
[0024] S2. Segment the deburring processin...
PUM
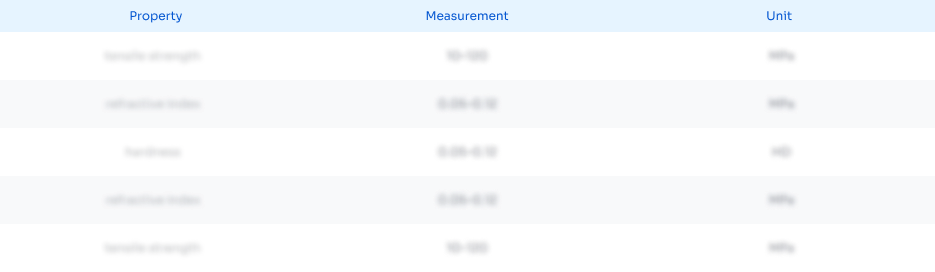
Abstract
Description
Claims
Application Information

- R&D
- Intellectual Property
- Life Sciences
- Materials
- Tech Scout
- Unparalleled Data Quality
- Higher Quality Content
- 60% Fewer Hallucinations
Browse by: Latest US Patents, China's latest patents, Technical Efficacy Thesaurus, Application Domain, Technology Topic, Popular Technical Reports.
© 2025 PatSnap. All rights reserved.Legal|Privacy policy|Modern Slavery Act Transparency Statement|Sitemap|About US| Contact US: help@patsnap.com