Structure and method for preventing gas blow-by during pouring of multi-component casting mold for sand-lined iron mold casting
A technology of iron mold sand-covered casting and mold pouring, which is applied in the direction of casting molding equipment, molds, mold components, etc., can solve the problems of unsafe production, air hole defects, gas explosion and blasting, etc., achieve good results and simplify production Operation process, the effect of improving production efficiency
- Summary
- Abstract
- Description
- Claims
- Application Information
AI Technical Summary
Problems solved by technology
Method used
Image
Examples
Embodiment Construction
[0024] The present invention will be further described in detail below in conjunction with the accompanying drawings and examples. The following examples are explanations of the present invention and the present invention is not limited to the following examples.
[0025] Example.
[0026] see Figure 1 to Figure 7 In this embodiment, the anti-channeling gas structure of the iron mold sand-coated casting multi-component casting mold includes an upper iron mold 7, a lower iron mold 8, an anti-channeling gas sand layer 1, two independent exhaust systems and a gas Partition system, one layer of anti-channeling gas-coated sand layer 1 is set on the parting plane of upper iron type 7 and lower iron type 8 respectively, and two independent exhaust systems and one gas partition system are arranged on the anti-channeling gas-coated layer 1 , the exhaust system includes an exhaust gap 2, an exhaust groove 3, and a plurality of exhaust holes 4 on the exhaust groove 3; the gas partition...
PUM
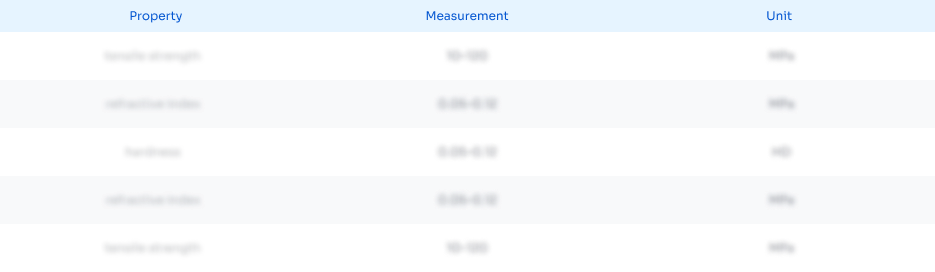
Abstract
Description
Claims
Application Information

- R&D Engineer
- R&D Manager
- IP Professional
- Industry Leading Data Capabilities
- Powerful AI technology
- Patent DNA Extraction
Browse by: Latest US Patents, China's latest patents, Technical Efficacy Thesaurus, Application Domain, Technology Topic, Popular Technical Reports.
© 2024 PatSnap. All rights reserved.Legal|Privacy policy|Modern Slavery Act Transparency Statement|Sitemap|About US| Contact US: help@patsnap.com