Data synchronization test device based on aeromagnetic superconducting full-tensor magnetic gradient measurement and control system
A measurement and control system and data synchronization technology, applied in the field of superconducting applications, can solve problems such as low synchronization accuracy, asynchronous full tensor magnetic data and position and attitude data, etc.
- Summary
- Abstract
- Description
- Claims
- Application Information
AI Technical Summary
Problems solved by technology
Method used
Image
Examples
Embodiment Construction
[0027] The aeronautical superconducting full-tensor magnetic gradient data acquisition and control system not only needs to collect full-tensor magnetic data, but also needs real-time position and attitude data corresponding to the full-tensor magnetic data, and the higher the synchronization, the better. The attitude data is used to effectively eliminate the interference introduced by the full tensor magnetic data in the moving state, and then the full tensor magnetic data after the interference is eliminated corresponds to the position information to obtain the spatial distribution information of the measured area. Therefore, the measurement accuracy of the position and attitude data and the synchronization with the full tensor magnetic data determine the data quality of the aeronautical superconducting full tensor magnetic gradient data acquisition and control system. The data sources are different, resulting in asynchronous full tensor magnetic data and position and attitud...
PUM
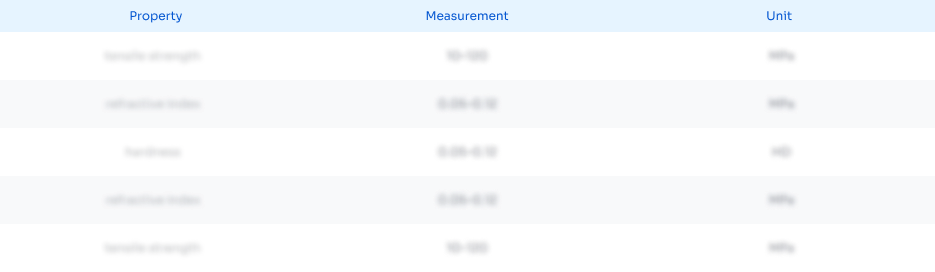
Abstract
Description
Claims
Application Information

- R&D Engineer
- R&D Manager
- IP Professional
- Industry Leading Data Capabilities
- Powerful AI technology
- Patent DNA Extraction
Browse by: Latest US Patents, China's latest patents, Technical Efficacy Thesaurus, Application Domain, Technology Topic, Popular Technical Reports.
© 2024 PatSnap. All rights reserved.Legal|Privacy policy|Modern Slavery Act Transparency Statement|Sitemap|About US| Contact US: help@patsnap.com