A multi-stage ladder-tooth type mixer for integrated afterburner
A technology of afterburner and mixer, applied in the direction of combustion chamber, continuous combustion chamber, combustion method, etc., which can solve the problems of affecting the combustion efficiency of afterburner, affecting the thrust performance of the engine, and high total pressure loss, etc. Achieve the effects of improving thermal mixing efficiency, suppressing noise, and reducing total pressure loss
- Summary
- Abstract
- Description
- Claims
- Application Information
AI Technical Summary
Problems solved by technology
Method used
Image
Examples
Embodiment Construction
[0021] The following embodiments will further illustrate the present invention in conjunction with the accompanying drawings.
[0022] The multi-stage ladder-tooth type mixer described in the embodiment of the present invention includes two-stage mixing sections, each stage of which is composed of ladder-tooth crown mixers of different sizes, figure 1 and 2 The three-dimensional view and the top view of the first-stage mixing section trapezoidal mixer according to the embodiment of the present invention. The ladder-tooth crown mixer is formed by installing closely arranged internal and external inclined ladder teeth on the outlet end face of the mixing section of each stage. When the gas flows through these staggered ladder tooth structures, the flow direction vortex is induced to strengthen the internal and external bypass airflow. blending. The structure of the first-stage blending section is similar to that of the ladder-tooth mixer in the second-stage blending section. ...
PUM
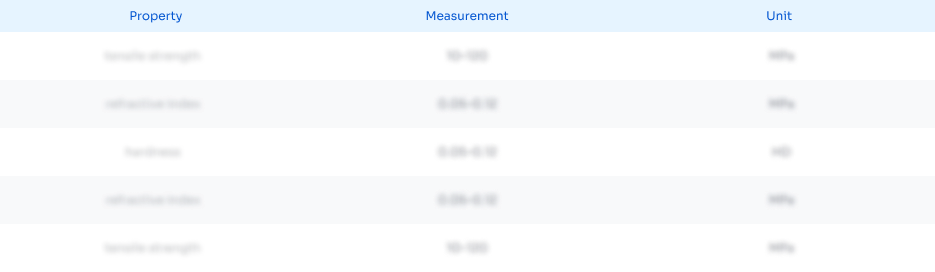
Abstract
Description
Claims
Application Information

- R&D
- Intellectual Property
- Life Sciences
- Materials
- Tech Scout
- Unparalleled Data Quality
- Higher Quality Content
- 60% Fewer Hallucinations
Browse by: Latest US Patents, China's latest patents, Technical Efficacy Thesaurus, Application Domain, Technology Topic, Popular Technical Reports.
© 2025 PatSnap. All rights reserved.Legal|Privacy policy|Modern Slavery Act Transparency Statement|Sitemap|About US| Contact US: help@patsnap.com