Stacking machine
A stacker and detection mechanism technology, applied in the direction of hoisting devices, lifting equipment safety devices, etc., can solve the problems of complex overall structure, high cost, and inconvenient maintenance and maintenance, and achieve high safety, rapid response, and simple structure Effect
- Summary
- Abstract
- Description
- Claims
- Application Information
AI Technical Summary
Problems solved by technology
Method used
Image
Examples
Embodiment Construction
[0058] The above solution will be further described below in conjunction with specific embodiments. It should be understood that these examples are used to illustrate the present invention and not to limit the scope of the present invention. The implementation conditions used in the examples can be further adjusted according to the conditions of specific manufacturers, and the implementation conditions not indicated are usually the conditions in routine experiments.
[0059] see figure 1 , which is a structural schematic diagram of an embodiment of the present invention, provides a stacker, including a base 1, a door frame mechanism 2 installed on the base 1, and a loader installed inside the door frame mechanism 2 and can be raised and lowered relative to the door frame mechanism 2. The object stage mechanism 3 and the lifting drive mechanism 5 which is transmission-connected with the object stage mechanism 3 to drive the object stage mechanism 3 to move up and down.
[006...
PUM
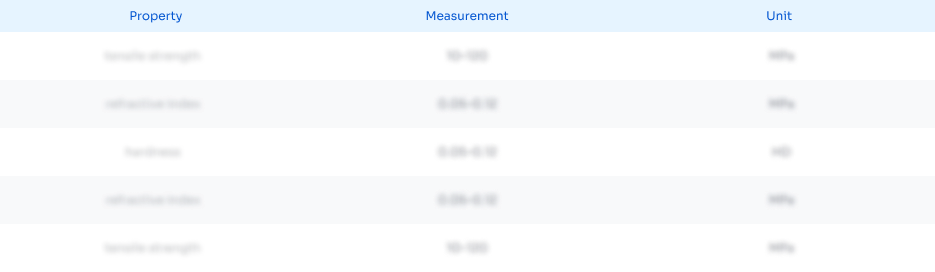
Abstract
Description
Claims
Application Information

- R&D
- Intellectual Property
- Life Sciences
- Materials
- Tech Scout
- Unparalleled Data Quality
- Higher Quality Content
- 60% Fewer Hallucinations
Browse by: Latest US Patents, China's latest patents, Technical Efficacy Thesaurus, Application Domain, Technology Topic, Popular Technical Reports.
© 2025 PatSnap. All rights reserved.Legal|Privacy policy|Modern Slavery Act Transparency Statement|Sitemap|About US| Contact US: help@patsnap.com