Multi-axis cooperative blind milling method for printed circuit board and device
A technology for printed circuit boards and circuit boards, which is applied in milling machine equipment, manufacturing tools, details of milling machine equipment, etc., can solve the problems that the depth of step grooves cannot be unified, the depth of product grooves cannot be realized, and the depth control accuracy is difficult to coordinate, etc. Positioning speed and paste speed, low cost, and the effect of improving efficiency
- Summary
- Abstract
- Description
- Claims
- Application Information
AI Technical Summary
Problems solved by technology
Method used
Image
Examples
Embodiment Construction
[0041] In order to make the above objects, features and advantages of the present invention more comprehensible, specific implementations of the present invention will be described in detail below. In the following description, numerous specific details are set forth in order to provide a thorough understanding of the present invention. However, the present invention can be implemented in many other ways different from those described here, and those skilled in the art can make similar improvements without departing from the connotation of the present invention, so the present invention is not limited by the specific implementation disclosed below.
[0042] see Figure 3 to Figure 5 As shown, as an embodiment of a multi-axis collaborative blind milling method for a printed circuit board, the following processing steps are included:
[0043] Pulling the platform: on the worktable 4 of the multi-axis milling machine, lay a backing plate 5 in the area corresponding to each spind...
PUM
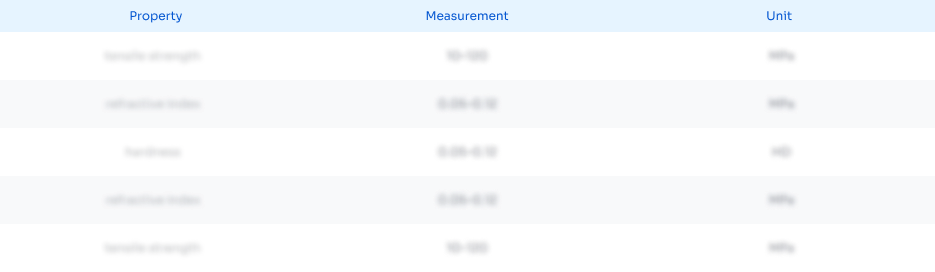
Abstract
Description
Claims
Application Information

- Generate Ideas
- Intellectual Property
- Life Sciences
- Materials
- Tech Scout
- Unparalleled Data Quality
- Higher Quality Content
- 60% Fewer Hallucinations
Browse by: Latest US Patents, China's latest patents, Technical Efficacy Thesaurus, Application Domain, Technology Topic, Popular Technical Reports.
© 2025 PatSnap. All rights reserved.Legal|Privacy policy|Modern Slavery Act Transparency Statement|Sitemap|About US| Contact US: help@patsnap.com