Automatic directional feeding robot for channel steel parts
A robot and material feeding technology, which is applied in the direction of vibrating conveyors, conveyors, conveyor objects, etc., can solve the problems of low efficiency and low degree of automation, and achieve the effects of high efficiency, convenient grasping and welding, and convenient sliding
- Summary
- Abstract
- Description
- Claims
- Application Information
AI Technical Summary
Problems solved by technology
Method used
Image
Examples
Embodiment 1
[0038] The automatic channel steel parts directional feeding robot of the present invention pours several channel steel parts into the vibrating plate assembly 2, and under the vibration feeding action of the vibrating plate assembly 2, the channel steel parts enter the conveying guide rail assembly 4 and pass through the miniature The vibration of the oscillator 3 transports forward and falls into the sliding material guide rail 5 .
[0039] Then, start the stepper motor 67, and the stepper motor 67 drives the ring gear 65 through the gear 68 to rotate the discharge disc 64 in the fixed ring 60-1 to work at a step angle of 90°.
[0040] When the channel steel piece with the opening facing upwards slides into the discharge groove 64-1, as the discharge plate 64 rotates 90°, the channel steel piece with the upward opening is turned over and buckled on the hanging protrusion 64-2, and at this time The discharge groove 64-1 of the discharge groove 62-1 is aligned with the distrib...
Embodiment 2
[0044]On the basis of Example 1, the inclination angle of the sliding guide rail 5 is +135°; the inclination angle of the feeding guide rail 7 is -135°; the fixed ring 60-1 is provided with a feeding hole 60-2 and the discharge hole 60-3, the feed hole 60-2 communicates with the sliding guide rail 5, and the discharge hole 60-3 communicates with the feed guide rail 7; The three discharge troughs 64-1 correspond to the coordinated work, and on the other hand facilitate the sliding of the channel steel parts.
[0045] The splitter core 62 is provided with a splitter groove 62-1, which ensures the stable discharge of the channel steel piece with the opening facing downward in the sliding material guide rail 5 after it turns over and lands on the hanging protrusion 64-2.
[0046] The discharge tray 64 is provided with a plurality of discharge troughs 64-1, and the discharge trough 64-1 is provided with a material hanging bump 64-2; it ensures that the channel steel piece with the ...
PUM
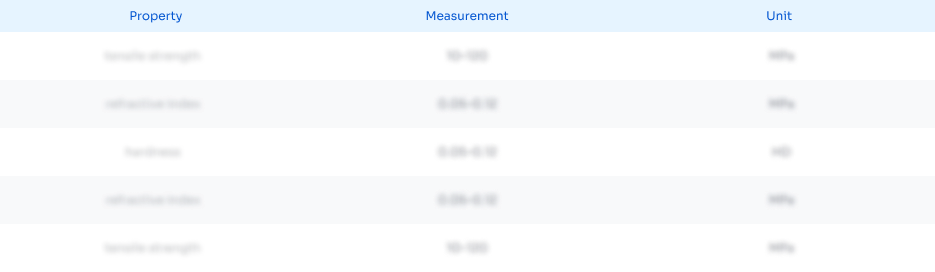
Abstract
Description
Claims
Application Information

- Generate Ideas
- Intellectual Property
- Life Sciences
- Materials
- Tech Scout
- Unparalleled Data Quality
- Higher Quality Content
- 60% Fewer Hallucinations
Browse by: Latest US Patents, China's latest patents, Technical Efficacy Thesaurus, Application Domain, Technology Topic, Popular Technical Reports.
© 2025 PatSnap. All rights reserved.Legal|Privacy policy|Modern Slavery Act Transparency Statement|Sitemap|About US| Contact US: help@patsnap.com