Double-robot force/position multivariate data driving method based on reinforcement learning
A technology of reinforcement learning and multivariate data, applied to manipulators, program-controlled manipulators, manufacturing tools, etc., to solve parameter optimization problems, improve dexterity, and avoid errors
- Summary
- Abstract
- Description
- Claims
- Application Information
AI Technical Summary
Problems solved by technology
Method used
Image
Examples
Embodiment Construction
[0047] In order to make the above objects, features, and advantages of the present invention, the technical solutions of the present invention will be described in detail below with reference to the accompanying drawings and specific examples. It should be noted that the described embodiments are merely the embodiments of the present invention, not all of the embodiments, based on the embodiments in the present invention, and those of ordinary skill in the art without creative labor premise Other embodiments belong to the scope of the invention.
[0048] Dual robots in the same station region synergistic, handling and flip, need to study the interaction of robots and the environment, and most common interactive control methods are force-position control. When the environment is unknown, the force / bit control is not sufficient to generate the uncertainty in the environment, and the force / bit control is required, and it is necessary to estimate its expected value.
[0049] Machi...
PUM
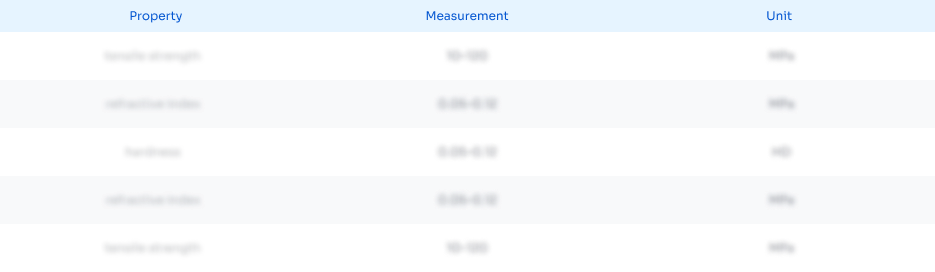
Abstract
Description
Claims
Application Information

- R&D Engineer
- R&D Manager
- IP Professional
- Industry Leading Data Capabilities
- Powerful AI technology
- Patent DNA Extraction
Browse by: Latest US Patents, China's latest patents, Technical Efficacy Thesaurus, Application Domain, Technology Topic, Popular Technical Reports.
© 2024 PatSnap. All rights reserved.Legal|Privacy policy|Modern Slavery Act Transparency Statement|Sitemap|About US| Contact US: help@patsnap.com