Double-fork shaft sleeve bearing automatic press-fitting system and assembling method
A double-forked shaft and bearing technology, which is applied in metal processing, metal processing equipment, manufacturing tools, etc., can solve the problems of complicated installation process, difficult to control accurately, and easily damaged bearings
- Summary
- Abstract
- Description
- Claims
- Application Information
AI Technical Summary
Problems solved by technology
Method used
Image
Examples
Embodiment 1
[0061] A specific embodiment of the present invention discloses an automatic press-fitting system for double-fork bushing bearings, which includes: a slide rail mechanism 4, a sliding clamp 5, a press-fitting mechanism 6 and a turning mechanism 7; wherein the sliding clamp 5 is used for Fix the double-pronged bushing 1, and the sliding fixture 5 can slide on the linear guide rail 41 of the slide rail mechanism 4; the turning mechanism 7 can clamp the double-pronged bushing 1 and turn it over; the press-fitting mechanism 6 is set on the slide rail mechanism 4, and the press-fit mechanism 6 is used to press-fit the bearing on the bifurcated bushing 1.
[0062] In the double-prong bushing bearing automatic press-fitting system of the present invention, the double-prong bushing 1 is installed on the sliding fixture 5, and the sliding fixture 5 is driven to linearly displace by the slide rail mechanism 4, and then the double-prong bushing 1 is paired by the press-fitting mechanism 6...
Embodiment 2
[0108] A specific embodiment of the present invention discloses an assembly method of a double-pronged bushing bearing. The double-pronged bushing bearing automatic press-fitting system in Embodiment 1 is used to press-fit the two-pronged bushing 1 to the bearings at both ends. Include the following steps:
[0109] Step S1: Drive the sliding fixture 5 to slide to the first station along the linear guide rail 41; when the sliding fixture 5 is in the first station, place the first bearing 2 on the bearing positioning tool 51, and place the double-fork bushing 1 on the second station A shaft sleeve positioning tool 52;
[0110] Step S2: Drive the sliding fixture 5 to slide to the second station along the linear guide rail 41; when the sliding fixture 5 is located at the second station, the press-fitting mechanism 6 drives the magnetic indenter 65 to move down, and the magnetic indenter 65 absorbs the second station by magnetic force. a bearing 2;
[0111] Step S3: Drive the sli...
PUM
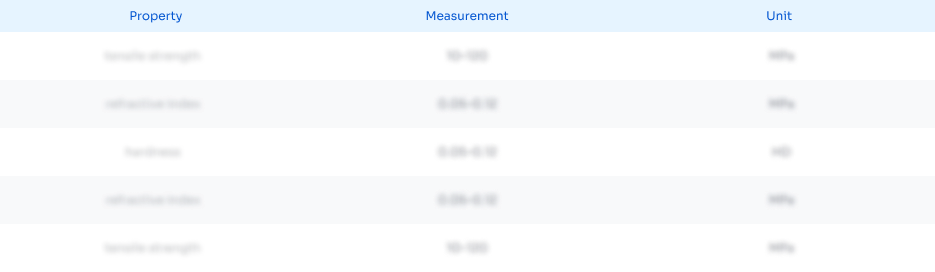
Abstract
Description
Claims
Application Information

- R&D
- Intellectual Property
- Life Sciences
- Materials
- Tech Scout
- Unparalleled Data Quality
- Higher Quality Content
- 60% Fewer Hallucinations
Browse by: Latest US Patents, China's latest patents, Technical Efficacy Thesaurus, Application Domain, Technology Topic, Popular Technical Reports.
© 2025 PatSnap. All rights reserved.Legal|Privacy policy|Modern Slavery Act Transparency Statement|Sitemap|About US| Contact US: help@patsnap.com