Driving method and driving circuit for piezoelectric ceramic actuator
A technology of piezoelectric ceramics and driving circuits, which is applied in the direction of piezoelectric effect/electrostriction or magnetostriction motors, generators/motors, instruments, etc., and can solve the problems that high precision and low ripple voltage output cannot be taken into account at the same time
- Summary
- Abstract
- Description
- Claims
- Application Information
AI Technical Summary
Problems solved by technology
Method used
Image
Examples
Embodiment 1
[0038] A piezoelectric ceramic actuator driving method 100, such as figure 1 shown, including:
[0039] Step 110, amplifying the input control signal according to the required amplification factor from the input voltage Vp to the target voltage V0 to obtain the pre-amplification control signal V1;
[0040] Step 120, amplify the sum of the pre-amplification control signal V1 and the feedback signal V2 to obtain the voltage control signal V4, wherein the feedback signal V2 is the output voltage V of the transformer T1 after it is discharged under the action of the input voltage Vp 0 'The signal obtained after resistive voltage division;
[0041] Step 130: Using the PWM control chip to output a PWM wave with a specific duty cycle and frequency under the combined action of the voltage control signal V4 and the feedback voltage V5, the primary coil stores or discharges energy under the action of the PWM wave and the inductance value of the transformer can, output voltage V when d...
Embodiment 2
[0047] A piezoceramic actuator drive circuit such as figure 2 As shown, it includes: a control signal pre-amplification module, a boost control module, a boost module, an unload control module, and an unload module. The control signal pre-amplification module is used to amplify the input control signal according to the amplification factor required from the input voltage Vp to the target voltage V0 to obtain the pre-amplification control signal V1; the boost control module is used for the pre-amplification control signal V1 and feedback The sum of the signal V2 is amplified to obtain the voltage control signal V4, and the feedback signal V2 is the output voltage V of the boost module 0 'The signal obtained after the resistor divides; the boost module includes a PWM control chip and a transformer T1, where the PWM control chip outputs a PWM wave with a specific duty cycle and frequency under the joint action of the voltage control signal V4 and the feedback voltage V5 , the p...
PUM
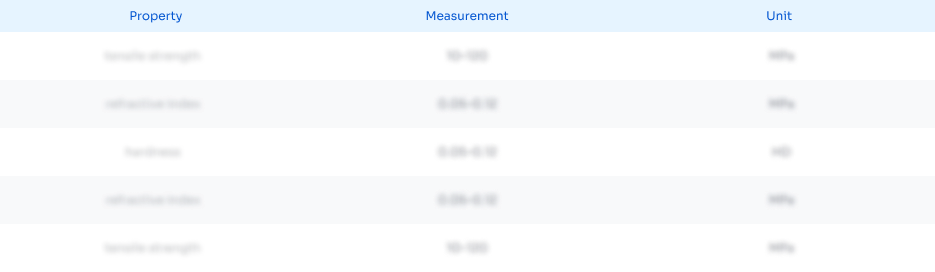
Abstract
Description
Claims
Application Information

- R&D
- Intellectual Property
- Life Sciences
- Materials
- Tech Scout
- Unparalleled Data Quality
- Higher Quality Content
- 60% Fewer Hallucinations
Browse by: Latest US Patents, China's latest patents, Technical Efficacy Thesaurus, Application Domain, Technology Topic, Popular Technical Reports.
© 2025 PatSnap. All rights reserved.Legal|Privacy policy|Modern Slavery Act Transparency Statement|Sitemap|About US| Contact US: help@patsnap.com