A Quick Docking Mechanism with Incomplete Constraints
A docking mechanism and fully constrained technology, applied in the direction of manipulators, manufacturing tools, etc., can solve the problems of high precision requirements in the pre-docking process, difficulty in popularization and application, and complex mechanisms, so as to achieve convenient and fast disconnection process, improve flexibility, and install The effect of simple structure
- Summary
- Abstract
- Description
- Claims
- Application Information
AI Technical Summary
Problems solved by technology
Method used
Image
Examples
Embodiment Construction
[0021] see Figure 1-Figure 2 , Figure 7 As shown, a fast docking mechanism with incomplete restraint includes an active docking joint 1 and a passive docking joint 2; 11 is driven to rotate, and the inner wall surface of the passive docking shell 20 of the passive docking joint 2 is processed with a card slot 21 matched with the self-locking device 12; The self-locking device 12 restricts the axial movement of the active butt joint 1 and the passive butt joint 2 .
[0022] see Figure 4 and Figure 5 As shown, preferably, the self-locking device 12 includes a wheel 120 and a ball 121; the outer peripheral side of the wheel 120 is fixed with a plurality of convex teeth 1201, and in the circumferential direction, one side of the convex tooth 1201 is an arc surface 1202, the other side of the protruding tooth 1201 is the elevation 1203, and the accommodating space for arranging the ball 121 is formed between the adjacent arc surface 1202 and the elevation 1203, and the side...
PUM
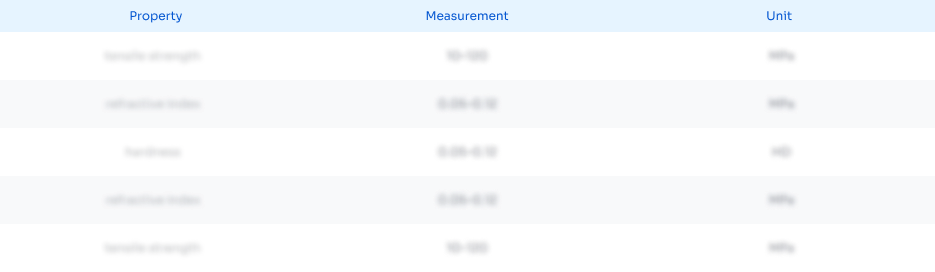
Abstract
Description
Claims
Application Information

- R&D
- Intellectual Property
- Life Sciences
- Materials
- Tech Scout
- Unparalleled Data Quality
- Higher Quality Content
- 60% Fewer Hallucinations
Browse by: Latest US Patents, China's latest patents, Technical Efficacy Thesaurus, Application Domain, Technology Topic, Popular Technical Reports.
© 2025 PatSnap. All rights reserved.Legal|Privacy policy|Modern Slavery Act Transparency Statement|Sitemap|About US| Contact US: help@patsnap.com