Method for determining fatigue load of refitted part of aircraft fuselage
An aircraft fuselage and fatigue load technology, applied in geometric CAD and other directions, can solve problems such as insufficient sample size, inability to effectively reflect the dispersion of fatigue loads, affecting the reliability of load data reliability and life assessment conclusions, etc., to improve effectiveness. , The effect of expanding the load sample library and saving the cost of load measurement
- Summary
- Abstract
- Description
- Claims
- Application Information
AI Technical Summary
Problems solved by technology
Method used
Image
Examples
Embodiment Construction
[0013] This invention method has been applied to the fuselage modification part 4 fatigue load determination work of a certain type of aircraft, such as figure 1 As shown, the aircraft fuselage includes a front fuselage 1 and a rear fuselage 2, and the wings 3 are connected to the aircraft fuselage. The embodiment refits the fuselage structure, and the fuselage modification part 4 is located on the rear fuselage 2. According to The inventive idea of the present application, to the method for determining the fatigue load of aircraft fuselage modification part 4, the original design parameters and refitting structural parameters of the known aircraft fuselage, and the historical flight parameter data after known modification of the aircraft, it is characterized in that it includes the following content :
[0014] 1) Add strain gauges 5 to the refitting part 4 of the aircraft fuselage, and obtain the measured strain data of the part through actual flight measurement;
[0015] ...
PUM
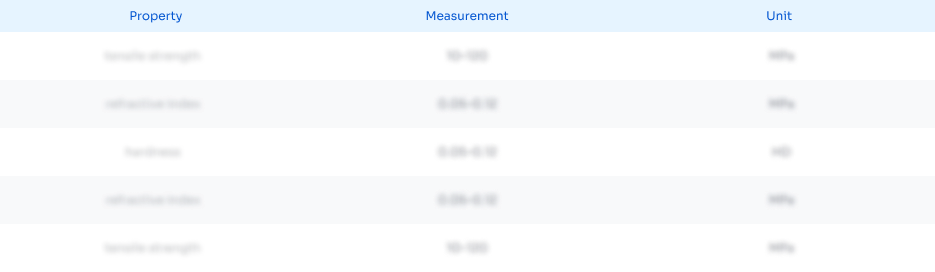
Abstract
Description
Claims
Application Information

- R&D Engineer
- R&D Manager
- IP Professional
- Industry Leading Data Capabilities
- Powerful AI technology
- Patent DNA Extraction
Browse by: Latest US Patents, China's latest patents, Technical Efficacy Thesaurus, Application Domain, Technology Topic, Popular Technical Reports.
© 2024 PatSnap. All rights reserved.Legal|Privacy policy|Modern Slavery Act Transparency Statement|Sitemap|About US| Contact US: help@patsnap.com