Multi-station rotary terminal crimping machine head
A terminal crimping, multi-station technology, used in circuit/collector parts, electrical components, connections, etc., can solve the problems of long waiting time for stamping, low stamping efficiency, etc., to improve production efficiency and achieve continuous and rapid stamping. Effect
- Summary
- Abstract
- Description
- Claims
- Application Information
AI Technical Summary
Problems solved by technology
Method used
Image
Examples
Embodiment Construction
[0028] In order to make the object, technical solution and advantages of the present invention clearer, the implementation manner of the present invention will be further described in detail below in conjunction with the accompanying drawings.
[0029] Such as figure 1 As shown, in the first embodiment of the multi-station rotary terminal crimping head of the present invention, the crimping head 100 includes a machine table 101, a support device 102 fixed on the machine table 101, and a The stamping head 200 on the device 102, the rotating seat 103 that is rotatably arranged on the machine platform 101, and the plurality of station seats 104 that are arranged on the rotating seat 103 and can rotate with the rotating seat 103, on the machine platform 101 A first driving motor 105 and a first right-angle reducer 106 are provided for driving the rotating base 103 to rotate.
[0030] When the multi-station rotary terminal crimping machine head 100 of the present invention is used...
PUM
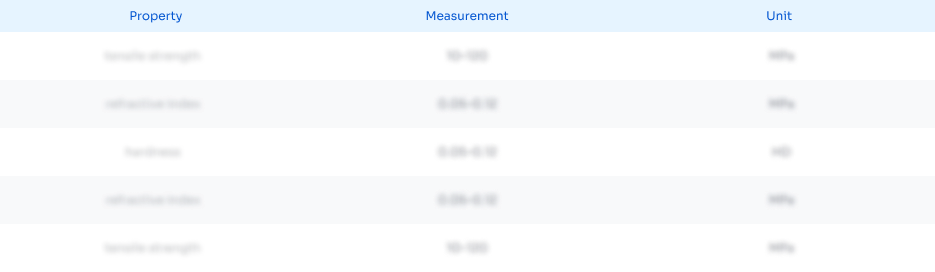
Abstract
Description
Claims
Application Information

- R&D
- Intellectual Property
- Life Sciences
- Materials
- Tech Scout
- Unparalleled Data Quality
- Higher Quality Content
- 60% Fewer Hallucinations
Browse by: Latest US Patents, China's latest patents, Technical Efficacy Thesaurus, Application Domain, Technology Topic, Popular Technical Reports.
© 2025 PatSnap. All rights reserved.Legal|Privacy policy|Modern Slavery Act Transparency Statement|Sitemap|About US| Contact US: help@patsnap.com