Bridge crane damping device
A technology of bridge cranes and shock absorbers, which is applied in the direction of springs/shock absorbers, mechanical equipment, traveling mechanisms, etc., and can solve problems such as safety accidents, damage to crane parts, and impact on the service life of the crane
- Summary
- Abstract
- Description
- Claims
- Application Information
AI Technical Summary
Problems solved by technology
Method used
Image
Examples
Embodiment 1
[0034] A bridge crane shock absorber, such as figure 1 As shown, it includes a crane. The crane includes a traveling end beam 1, a shock absorber 2, a main girder 3, a lifting truck 4, a hydraulic valve mechanism and an oil pressure plug mechanism. The traveling end beam 1 is set to two, and the two traveling end beams Beams 1 are respectively arranged on two rails, two shock absorbers 2 are arranged, the lower sides of the two shock absorbers 2 are respectively fixedly connected to the upper sides of the two traveling end beams 1, and the two ends of the main beam 3 are respectively arranged Above the two damping chambers 2, the lifting truck 4 is arranged on the upper side of the main beam 3, and the lifting truck 4 can move left and right on the upper side of the main beam 3. Cavity 201, the hydraulic cavity 201 is set as a cylindrical cavity, the hydraulic cavity 201 is filled with hydraulic oil, the hydraulic valve mechanism is set at the center position inside the hydrau...
PUM
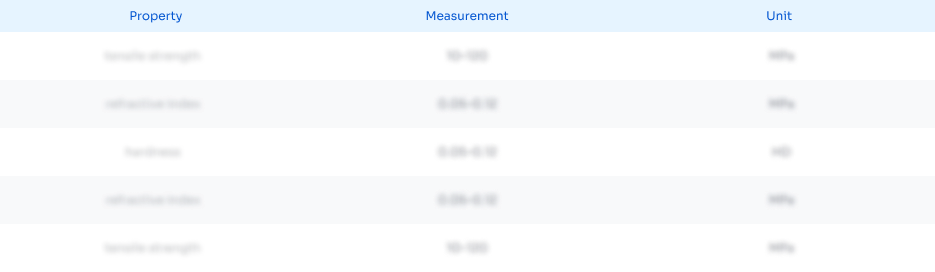
Abstract
Description
Claims
Application Information

- R&D
- Intellectual Property
- Life Sciences
- Materials
- Tech Scout
- Unparalleled Data Quality
- Higher Quality Content
- 60% Fewer Hallucinations
Browse by: Latest US Patents, China's latest patents, Technical Efficacy Thesaurus, Application Domain, Technology Topic, Popular Technical Reports.
© 2025 PatSnap. All rights reserved.Legal|Privacy policy|Modern Slavery Act Transparency Statement|Sitemap|About US| Contact US: help@patsnap.com